[Tube mill production line]Exploring the Innovations and Efficiency of Tube Mill Production Lines in Modern Manufacturing
News 2024-8-28
In today’s fast-paced manufacturing environment, efficiency, precision, and innovation are critical components of production systems. One such system that has gained significant attention over the years is the tube mill production line. This technology plays a vital role in the fabrication of pipes and tubes which are essential components in various industries, including construction, automotive, oil and gas, and more. Understanding the intricacies of a tube mill production line not only sheds light on its importance in manufacturing but also highlights the innovations that continuously evolve this technology.
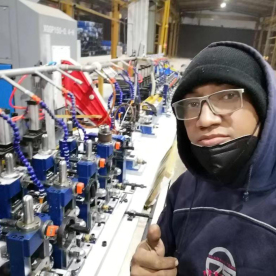
Exploring the Innovations and Efficiency of Tube Mill Production Lines in Modern Manufacturing
Once the tube has been formed, the next critical process is welding. A high-frequency induction welding system or an electric resistance welding (ERW) method is often employed. In the case of high-frequency welding, the tubes are heated to the necessary temperature to form a strong bond without adding additional material. This process is fast, efficient, and produces a strong welded seam that significantly improves the tube’s integrity. Quality control is paramount during this phase, as even minor discrepancies in welding can compromise the durability of the final product.
The tube mill production line does not stop at welding; it continues with processes such as sizing and cutting. The newly formed tubes pass through sizing rollers that ensure they meet the exact dimensions specified. This precision is critical, particularly in industries where the tubes must fit seamlessly into existing structures or systems. Following this, the tubes are cut to specified lengths, ready for packaging and shipment.
One of the most compelling aspects of modern tube mill production lines is the integration of automation and advanced technology. Industry 4.0 principles are becoming increasingly prevalent within manufacturing, leading to the incorporation of smart technologies such as the Internet of Things (IoT), big data analytics, and artificial intelligence. These innovations allow for real-time monitoring of production processes, which enhances operational efficiency and reduces waste. For instance, sensors can be embedded along the production line to monitor temperature, pressure, and material quality, providing valuable data that helps in predictive maintenance and quality assurance.
Moreover, manufacturers are realizing the importance of sustainability in production. Advances in tube mill technology have led to more energy-efficient machines that reduce the carbon footprint of the manufacturing process. Techniques such as using scrap metal in the production of new tubes not only help efficiency but also align with global sustainability goals. As industries strive to meet environmental regulations and consumer demands for greener products, the tube mill production line is evolving to become more eco-friendly.
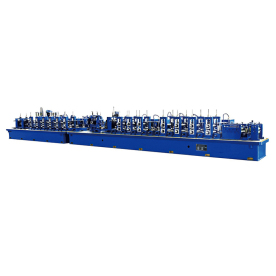
Exploring the Innovations and Efficiency of Tube Mill Production Lines in Modern Manufacturing
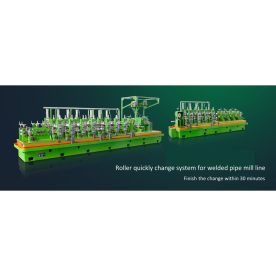
Exploring the Innovations and Efficiency of Tube Mill Production Lines in Modern Manufacturing
In conclusion, the tube mill production line represents a significant advancement in the manufacturing of tubes and pipes. Its combination of technology, efficiency, and adaptability ensures that it is an invaluable component of modern industrial production. As manufacturers continue to innovate and push the boundaries of technology, the future of tube mill production lines looks promising, with the potential for even greater efficiencies and capabilities. Understanding this technology not only highlights its current importance but also prepares industries for the next wave of manufacturing advancements. The production line is not just about creating tubes; it's about creating solutions for a wide array of challenges faced in various sectors of the economy.