[High frequency welder machine]Understanding the Benefits and Applications of High Frequency Welder Machines in Modern Manufacturing Processes
News 2024-8-27
High frequency welder machines have revolutionized the manufacturing industry by providing efficient, reliable, and high-quality welding solutions. These machines utilize high-frequency electrical energy to create welds in various materials, particularly thermoplastics and thin sheets of metals. Their versatility and speed have made them a fundamental tool in multiple sectors, including automotive, packaging, and textile industries. This article explores the workings, benefits, and applications of high frequency welder machines.
How High Frequency Welder Machines Work
High frequency welding involves the use of electromagnetic energy to heat materials to their melting point, allowing them to fuse together. The process begins when the welder machine generates a high-frequency electrical signal, which is usually in the range of 27.12 MHz. This electrical energy is directed through electrodes that are placed around the material to be welded.
When the high-frequency current passes through, it produces heat in the material due to the resistance encountered, effectively melting the surfaces of the materials being joined. The close control of temperature and pressure during this process ensures that the weld is clean and strong. After the materials reach the melting point, an external pressure is applied to them, allowing them to bond effectively as they cool and solidify.
Benefits of High Frequency Welder Machines
1. **Speed**: One of the most significant advantages of high frequency welder machines is their speed. The use of high-frequency energy allows for quick heating and welding, making these machines highly efficient for large-scale production. In industries where time is of the essence, such as automotive manufacturing, every second saved can lead to significant cost reductions.
2. **Precision**: High frequency welding is highly controllable, allowing manufacturers to achieve precise and consistent welds. This precision is crucial in applications where joint quality directly impacts product performance, such as in automotive components or electrical housings.
3. **Versatility**: These machines can weld a wide variety of materials, including different types of plastics, metals, and even textile materials. Their adaptability makes them suitable for numerous applications and facilitates the production of diverse products without needing multiple types of welding equipment.
4. **Cost-Effectiveness**: The efficiency and speed of high frequency welding reduce labor costs while increasing production output. Additionally, the process creates strong and durable welds, which can lead to lower product failure rates and reduced warranty claims, further driving down costs for manufacturers.
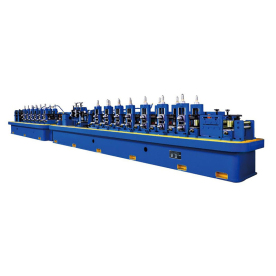
Understanding the Benefits and Applications of High Frequency Welder Machines in Modern Manufacturing Processes
Applications of High Frequency Welder Machines
1. **Automotive Industry**: In automotive manufacturing, high frequency welders are used for applications such as welding dashboards, fuel tanks, and other plastic components. Their ability to join thermoplastics with high precision increases overall product quality.
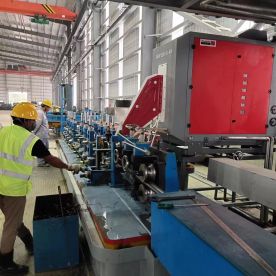
Understanding the Benefits and Applications of High Frequency Welder Machines in Modern Manufacturing Processes
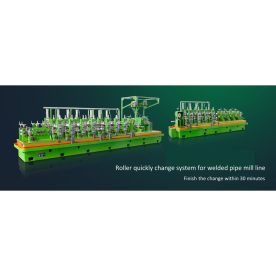
Understanding the Benefits and Applications of High Frequency Welder Machines in Modern Manufacturing Processes
4. **Medical Devices**: The medical industry utilizes high frequency welding for assembling medical devices and packaging that must maintain sterility. The precision and clean process of high frequency welding are invaluable in this field, where product integrity is paramount.
5. **Electrical Connectors**: High frequency welding techniques are deployed in creating reliable electrical connectors and components, ensuring efficient and robust connections in electronic devices.
Conclusion
High frequency welder machines have established themselves as indispensable tools in various industries due to their unique advantages in speed, precision, cost-effectiveness, and versatility. As manufacturing processes continue to evolve and the demand for high-quality products grows, these machines will likely play an integral role in shaping the future of production. Their ability to adapt to different materials and applications positions them as a cutting-edge solution for manufacturers worldwide. Adopting high frequency welding technology is a strategic move for companies looking to enhance their productivity and maintain a competitive edge in today’s fast-paced industrial landscape.