[Precision Mould for Tube Mills]Exploring the Advantages of Precision Mould for Tube Mills: Enhancing Efficiency and Quality in Metal Fabrication
News 2024-8-26
In the evolving landscape of metal fabrication, tube mills have become integral to various industries, including automotive, construction, and oil and gas. As demand for high-quality welded and seamless tubes continues to surge, the importance of precision tools and technologies, such as precision moulds, cannot be overstated. Precision mould for tube mills plays a critical role in enhancing the manufacturing process, ensuring that products meet the required standards while optimizing production efficiency. This article delves into the significance of precision moulds in tube mills, their types, benefits, and the future of this technology.
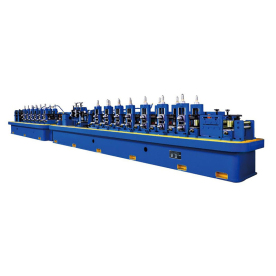
Exploring the Advantages of Precision Mould for Tube Mills: Enhancing Efficiency and Quality in Metal Fabrication
Tube mills are specialized machines used for the production of tubes and pipes from metal coils. The process involves several key stages, including slitting, forming, welding, and finishing. As materials pass through the tube mill, they are shaped into a tubular form before being welded to create a continuous length. This high-speed, continuous process benefits from precision moulds that ensure accurate dimensions and superior weld quality, ultimately leading to reduced waste and enhanced product performance.
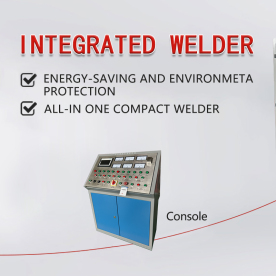
Exploring the Advantages of Precision Mould for Tube Mills: Enhancing Efficiency and Quality in Metal Fabrication
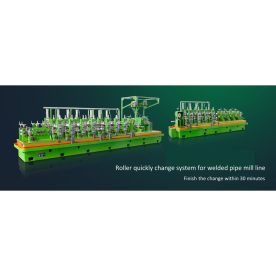
Exploring the Advantages of Precision Mould for Tube Mills: Enhancing Efficiency and Quality in Metal Fabrication
Types of Precision Moulds
There are several types of precision moulds used in tube mills, each tailored for specific applications:
1. **Open Moulds**: These are typically simpler in design and allow for the direct shaping of metal coils into tubes. While effective for certain applications, open moulds may not provide the same level of dimensional control as more complex designs.
2. **Closed Moulds**: These moulds provide a more controlled environment for shaping the metal, incorporating features that prevent distortion and ensure tight tolerances. Closed moulds are ideal for high-precision applications where the quality of the end product is critical.
3. **Interchangeable Moulds**: Many modern tube mills utilize interchangeable moulds, allowing manufacturers to switch between different designs with relative ease. This flexibility is essential for companies looking to adapt quickly to market demands while minimizing downtime.
Benefits of Using Precision Moulds
The adoption of precision moulds in tube mills brings a host of advantages that directly impact the quality and efficiency of the production process:
1. **Improved Quality**: Precision moulds help eliminate variations in tube dimensions, leading to higher quality products that meet or exceed industry standards. This improvement is particularly significant in industries where safety and reliability are paramount.
2. **Reduced Waste**: By ensuring precise dimensions and welds, precision moulds help minimize material wastage. This reduction not only decreases costs but also aligns with sustainability goals, supporting a more environmentally friendly manufacturing process.
3. **Enhanced Production Efficiency**: With precision moulds, tube mills can operate at higher speeds without sacrificing quality. This enhanced efficiency translates to increased output, enabling manufacturers to meet growing demand.
4. **Cost-Effectiveness**: Although the initial investment in precision mould technology may be higher than traditional options, the long-term savings from reduced waste and increased efficiency quickly offset these costs. Additionally, higher-quality products often command better market prices.
The Future of Precision Moulds in Tube Mills
As technology continues to advance, the future of precision moulds in tube mills looks promising. Innovations such as additive manufacturing, smart materials, and real-time monitoring systems are set to transform how precision moulds are designed and utilized. These advancements will further enhance the efficiency of tube mills and the quality of the products they produce.
In summary, precision moulds for tube mills are a crucial element of modern metal fabrication. By enhancing quality, reducing waste, and improving production efficiency, precision moulds enable manufacturers to respond effectively to the ever-increasing demands of their industries. As technology continues to advance, the role of precision moulds will only become more significant, driving innovation and excellence in tube manufacturing.