[High frequency welder]Exploring the Advantages and Innovations of High Frequency Welders in Modern Manufacturing Processes
News 2024-8-26
In the ever-evolving world of manufacturing, high frequency welding has emerged as a pivotal technique, revolutionizing various industries by offering a reliable and efficient method for joining materials. High frequency welders operate by utilizing electromagnetic energy to create heat within the materials being joined, ensuring a strong bond while minimizing the risk of material distortion. This technology has gained traction across sectors ranging from automotive to textile and packaging, owing to its remarkable efficiency and versatility.
**Understanding High Frequency Welding**
At its core, high frequency welding—also known as high frequency induction welding—relies on the principle of generating heat through electromagnetic induction. This process involves placing two materials in close proximity to an alternating current (AC) electromagnetic field. As the current flows through the materials, it induces eddy currents, which generate heat due to the resistance of the material. The localized heating approach allows for precise control over the welding process, resulting in high-quality welds with minimal thermal alteration to the surrounding materials.
**Applications of High Frequency Welders**
One of the most significant advantages of high frequency welding is its versatility. It finds applications in multiple industries, including:
1. **Automotive Industry**: High frequency welders are extensively used in the automotive sector for fabricating exhaust systems, body panels, and structural components. Their ability to create strong, lightweight joints contributes significantly to vehicle performance and safety.
2. **Textile Industry**: In manufacturing textiles, high frequency welding is employed to bond materials such as PVC and PU. This method eliminates the need for traditional stitching, thereby enhancing the durability of products like waterproof clothing and tarpaulins.
3. **Packaging**: The food and beverage industry benefits from high frequency welding in the creation of vacuum-sealed packaging. The strength and sealing quality achieved through this method help preserve products while extending their shelf life.
4. **Electrical and Electronics**: High frequency welders are used in producing wire harnesses and cable assemblies, ensuring reliable connections that are crucial for electronic applications.
**Advantages of High Frequency Welders**
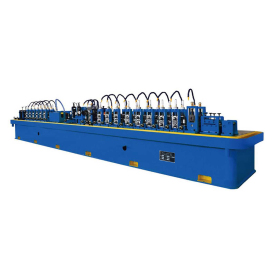
Exploring the Advantages and Innovations of High Frequency Welders in Modern Manufacturing Processes
1. **Speed and Efficiency**: High frequency welding processes are fast, with minimal set-up time required. As a result, manufacturers can significantly increase their output while reducing production time.
2. **Quality and Strength**: The localized heating offered by high frequency welding ensures strong and precise joints, making it an ideal choice for critical applications where quality cannot be compromised.
3. **Reduced Material Waste**: The accuracy of the process minimizes waste, as materials are welded together without the need for additional bonding agents or fillers, leading to cost savings and more sustainable manufacturing practices.
4. **Compatibility with Various Materials**: High frequency welding can be applied to a range of materials, including plastic, metal, and composites, making it an attractive option for diverse manufacturing needs.
5. **Minimal Thermal Impact**: The targeted heating method reduces the risk of warping or other thermal damage to adjacent materials, ensuring that the structural integrity of the parts is maintained.
**Innovations in High Frequency Welding Technology**
As the demand for efficiency and precision in manufacturing continues to grow, so does the innovation in high frequency welding technology. Modern systems are increasingly equipped with advanced features such as:
- **Automation and Integration**: Many high frequency welding machines now offer automation capabilities, allowing seamless integration into larger manufacturing systems. This increases operational efficiency while reducing labor costs.
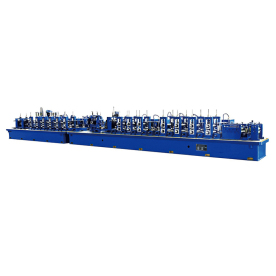
Exploring the Advantages and Innovations of High Frequency Welders in Modern Manufacturing Processes
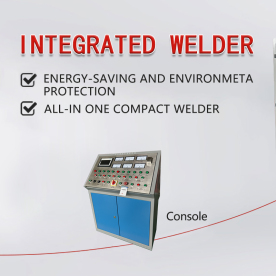
Exploring the Advantages and Innovations of High Frequency Welders in Modern Manufacturing Processes
- **Software Advances**: Sophisticated software solutions enable manufacturers to program and optimize welding parameters, leading to consistent and repeatable results.
In conclusion, high frequency welders represent a significant advance in manufacturing technology, providing efficient and effective solutions for joining materials across a range of industries. Their increasing adoption is a testament to their versatility, speed, and overall effectiveness. As innovations continue to emerge in this field, high frequency welding is poised to remain a critical component of modern manufacturing processes, helping businesses achieve their goals while meeting the demands of an increasingly competitive marketplace.