[Pipe mill production line with quality control measures]Ensuring Excellence in Pipe Manufacturing: An In-depth Look at Pipe Mill Production Line with Quality Control Measures
News 2024-8-26
In the world of manufacturing, the importance of quality control can never be overstated, particularly in the production of pipes that serve various applications in industries such as construction, automotive, and oil and gas. A pipe mill production line is a complex assembly of processes that transform raw materials into final products. Implementing stringent quality control measures is essential at every stage of this production line to ensure that the pipes meet required specifications and safety standards.
Understanding the Pipe Mill Production Line
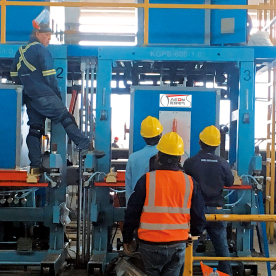
Ensuring Excellence in Pipe Manufacturing: An In-depth Look at Pipe Mill Production Line with Quality Control Measures
1. **Material Preparation**: The process begins with the selection and procurement of raw materials, which includes steel strips or plates. These materials undergo stringent quality checks to verify their chemical composition, tensile strength, and other essential properties. Utilizing high-quality raw materials is the foundation of quality pipe production.
2. **Forming**: Once the materials are prepared, the strips are fed into forming machines, where they are subjected to various processes such as bending, rolling, and shaping. The forming stage is critical because any defects introduced here can propagate through the subsequent stages. Therefore, precision equipment and skilled operators are essential.
3. **Welding**: After the forming process, the edges of the strips are welded together to create a continuous pipe. This stage often employs different welding techniques, including electric resistance welding (ERW) or submerged arc welding (SAW). Quality control during welding is paramount, as the welds must be strong enough to withstand operational pressures. Automated ultrasonic testing is frequently employed to detect any imperfections in the welds.
4. **Heat Treatment**: Post-welding, heat treatment is applied to relieve stresses introduced during the welding process and to enhance the material properties of the pipe. Quality control measures involve monitoring temperature and time during this critical phase, as variations can lead to inconsistencies in strength and ductility.
5. **Surface Finishing**: After heat treatment, pipes often undergo surface finishing processes such as grinding, polishing, or coating. This stage not only improves aesthetics but also enhances the corrosion resistance of the pipes. Quality assessments are performed using methods such as visual inspections and thickness measurements to ensure that surface treatments meet industry standards.
6. **Inspection and Testing**: The final stage of the pipe mill production line involves comprehensive inspection and testing. Pipes are usually subjected to non-destructive testing (NDT) methods, such as radiography, magnetic particle inspection, and hydrostatic testing. These tests are designed to identify any flaws or weaknesses that could compromise the pipe's performance in real-world applications.
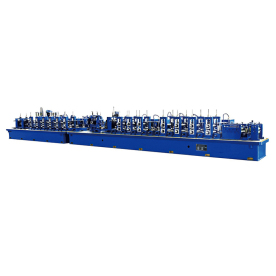
Ensuring Excellence in Pipe Manufacturing: An In-depth Look at Pipe Mill Production Line with Quality Control Measures
Quality control measures are the backbone of any pipe mill production line. They not only ensure that the final products adhere to regulatory standards but also enhance customer satisfaction and reduce costly rework. Several key quality control strategies can be employed throughout the production process:
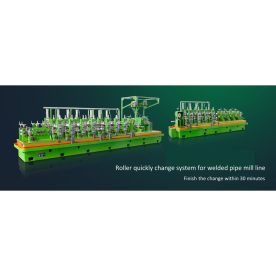
Ensuring Excellence in Pipe Manufacturing: An In-depth Look at Pipe Mill Production Line with Quality Control Measures
- **Training and Certification**: Ensuring that operators and inspectors are well trained and certified in their respective roles enhances the overall quality of the production line. Regular training keeps personnel updated on the latest technologies and best practices.
- **Regular Equipment Calibration**: Machinery and testing equipment used in the production line must be calibrated regularly. This practice minimizes errors and ensures precise manufacturing and testing.
- **Data Analysis and Continuous Improvement**: Implementing statistical process control (SPC) can help monitor key parameters and identify trends that could lead to failures. By analyzing this data, manufacturers can adopt a continuous improvement approach that enhances quality over time.
- **Customer Feedback**: Ultimately, the end-users of the pipes provide critical insights into product performance. Establishing a feedback loop helps manufacturing teams understand areas for improvement and innovate accordingly.
Conclusion
In the highly competitive field of pipe manufacturing, the implementation of rigorous quality control measures within the pipe mill production line is indispensable. It ensures that every pipe is strong, reliable, and safe for use across various applications. By investing in quality assurance at every step—from raw material selection to final inspection—manufacturers not only build a reputation for excellence but also contribute to the safety and reliability of the infrastructure that relies on their products. Ultimately, a commitment to quality is a commitment to success in the ever-evolving manufacturing landscape.