[High-efficiency ERW tube mill]Unlocking the Future of Manufacturing: High-Efficiency ERW Tube Mill Technology Transforms Steel Processing and Industry Standards
News 2024-8-25
In the ever-evolving landscape of manufacturing, the quest for efficiency and precision has paved the way for numerous innovations, particularly within industries reliant on steel processing. Among those innovations, the High-Efficiency Electric Resistance Welding (ERW) tube mill stands out as a revolutionary technology that not only enhances production rates but also significantly improves the quality of finished products. This article delves into the intricate workings of high-efficiency ERW tube mills, their advantages in the manufacturing sector, and their potential to redefine industry standards.
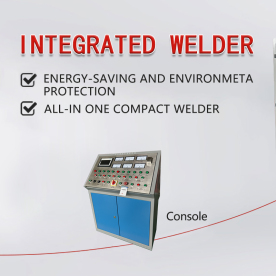
Unlocking the Future of Manufacturing: High-Efficiency ERW Tube Mill Technology Transforms Steel Processing and Industry Standards
One of the key advantages of using a high-efficiency ERW tube mill is the significant energy efficiency it offers. Traditional welding methods are often energy-intensive, leading to increased operational costs. In contrast, the ERW process consumes considerably less energy, aligning with the growing global emphasis on sustainability and eco-friendly manufacturing practices. The reduced energy requirement not only reflects an immediate cost benefit but also contributes to a lower carbon footprint, appealing to an increasingly eco-conscious market.
Moreover, high-efficiency ERW tube mills exhibit enhanced production speeds. Modern advancements in technology have facilitated the development of mills capable of producing large volumes of tubes in a shorter timeframe. This is particularly beneficial for industries where demand fluctuates or for projects that require a quick turnaround. With the capability to produce high-quality steel tubes at an impressive rate, manufacturers can significantly improve their overall operational efficiency, allowing them to meet market demands promptly.
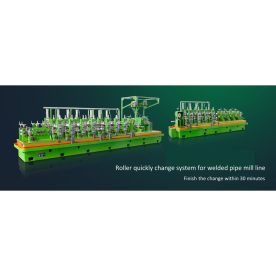
Unlocking the Future of Manufacturing: High-Efficiency ERW Tube Mill Technology Transforms Steel Processing and Industry Standards

Unlocking the Future of Manufacturing: High-Efficiency ERW Tube Mill Technology Transforms Steel Processing and Industry Standards
Furthermore, the adaptability of high-efficiency ERW tube mills allows manufacturers to produce a diverse range of tube dimensions and specifications. This versatility is vital in today’s market, where customization and specific client requirements are increasingly common. By adjusting parameters on the fly, manufacturers can cater to diverse projects, reducing lead times and minimizing material waste.
In conclusion, the high-efficiency ERW tube mill presents an unprecedented opportunity for the manufacturing sector to enhance productivity, reduce costs, and improve sustainability. Its innovation not only redefines traditional welding and forming processes but also meets the pressing demands of modern industries. As technology continues to advance, the role of high-efficiency ERW tube mills will undoubtedly expand, shaping the future of steel processing and setting new standards in manufacturing excellence. Companies ready to embrace this technology will find themselves at the forefront of an industry transformation, equipped to tackle the challenges and opportunities of the evolving global landscape.