[Solid state high frequency welder]Understanding the Benefits and Applications of Solid State High Frequency Welders in Modern Manufacturing Processes
News 2024-8-24
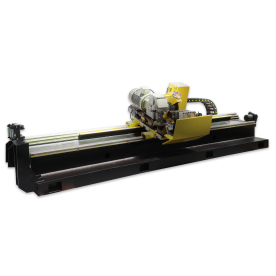
Understanding the Benefits and Applications of Solid State High Frequency Welders in Modern Manufacturing Processes
What is a Solid State High Frequency Welder?
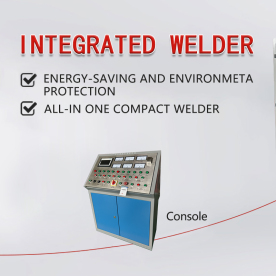
Understanding the Benefits and Applications of Solid State High Frequency Welders in Modern Manufacturing Processes
The heart of a solid-state welder lies in its solid-state components, such as transistors and diodes, which offer several advantages over conventional equipment. These components allow for precise control of the welding process, resulting in a stronger and more consistent weld. Furthermore, solid-state technology tends to be more energy-efficient and has a longer operational lifespan, making it a cost-effective solution for manufacturers.
Benefits of Solid State High Frequency Welders
1. **Increased Efficiency**: Solid state high frequency welders are designed to deliver quick and efficient welding processes. They can achieve higher welding speeds, which leads to increased productivity on the manufacturing floor. Because these machines can operate at higher frequencies, they can weld thinner materials without sacrificing quality.
2. **Improved Precision and Control**: The use of solid-state technology allows for more precise control over the welding parameters, such as current and time. This level of control ensures that the welds produced are consistent, reducing the likelihood of defects and rework. The ability to finely tune settings allows operators to work with a wide range of materials and thicknesses.
3. **Greater Versatility**: Solid state welders are versatile tools that can be used for various applications. From automotive components to electronics and metal fabrication, the adaptability of these machines makes them suitable for a diverse range of industries. Their ability to handle different materials, including ferrous and non-ferrous metals, expands their applicability even further.
4. **Energy Efficiency**: The efficiency of solid state welders translates into energy savings for manufacturers. These machines tend to consume less power than traditional welding systems, contributing to lower operational costs. Given the rising cost of energy, using more energy-efficient equipment is a practical consideration for manufacturers aiming to improve their bottom line.
5. **Reduced Maintenance**: A solid state welder typically requires less maintenance compared to its vacuum tube counterparts. The solid-state components are less prone to wear and tear, leading to lower downtime and maintenance costs. This reliability ensures that manufacturers can maintain productivity levels without frequent interruptions.
Applications of Solid State High Frequency Welders
The applications of solid state high frequency welders are vast and varied. Here are some common industries and uses:
- **Automotive Manufacturing**: In the automotive sector, solid state welders are used for welding components such as battery packs, wiring harnesses, and subassemblies. The need for speed and reliability in automotive production processes makes these machines ideal for such applications.

Understanding the Benefits and Applications of Solid State High Frequency Welders in Modern Manufacturing Processes
- **Metal Fabrication**: Metal fabricators utilize solid state welders to produce high-quality welds in a range of metal components. Their ability to handle thin materials makes them particularly useful in fabrication shops that work with delicate panels and parts.
- **Aerospace**: In the aerospace industry, where the margin for error is minimal, the precision of solid state high frequency welders is essential. They are employed in the manufacturing of lightweight components and assemblies necessary for aircraft.
Conclusion
Solid state high frequency welders represent a significant advancement in welding technology, bringing efficiency, precision, and versatility to modern manufacturing processes. As industries continue to evolve and manufacturers strive for higher standards of quality and productivity, the reliance on solid state welding technology is likely to grow. By incorporating these innovative machines into their operations, manufacturers can not only enhance their production capabilities but also position themselves for success in an increasingly competitive market.