[All-in-one high frequency welder]Exploring the Versatility and Efficiency of the All-in-One High Frequency Welder for Metal Fabrication Industries
News 2024-8-23
****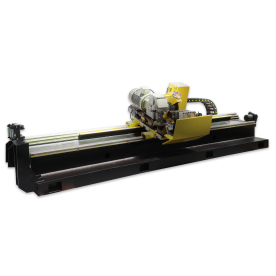
Exploring the Versatility and Efficiency of the All-in-One High Frequency Welder for Metal Fabrication Industries
High frequency welding, often utilized for pipe and tube fabrication, employs high-frequency electrical currents to create heat through resistance. This heat is then used to join metal parts together, providing a strong and efficient bond. The all-in-one high frequency welder takes this established method and expands upon it by incorporating multiple welding processes into one unit. This unique feature allows operators to switch between welding methods without the need to invest in additional machinery, making it ideal for businesses looking to streamline their operations.
One of the most noteworthy advantages of an all-in-one high frequency welder is its capability to support various welding techniques. For instance, it is adept at both TIG (Tungsten Inert Gas) and MIG (Metal Inert Gas) welding. This versatility enables fabricators to tackle a wide array of projects with differing requirements, from thin sheets to heavier materials. By integrating multiple welding methods into one device, industries can reduce the need for various welding machines, saving both floor space and capital investment.
Moreover, the all-in-one high frequency welder is designed to maximize efficiency and minimize downtime. Traditional welding setups often require significant time for machine calibration or configuration changes, potentially leading to delays in production schedules. In contrast, this high-frequency machine allows for rapid transitions and set-ups, empowering operators to quickly adapt to changing specifications or project demands. This operational flexibility can translate into a more agile manufacturing process, allowing companies to react faster to market needs and client requests.
The improved control and precision offered by high frequency welders is another reason for their increasing popularity. Advanced digital controls and programmed settings enable operators to achieve consistent and repeatable welds. This eliminates variability that can arise from manual welding processes, thereby enhancing overall quality. The result is stronger welds with less rework needed, which is a crucial factor in maintaining project timelines and budget constraints.
Furthermore, the integration of technology into the all-in-one high frequency welder allows for real-time monitoring and diagnostics. Many of these machines come equipped with software that can track performance data, providing operators with insights into their welding processes. This data can be invaluable in identifying areas for improvement or addressing issues before they escalate, leading to reduced scrap rates and enhanced operational efficiency.
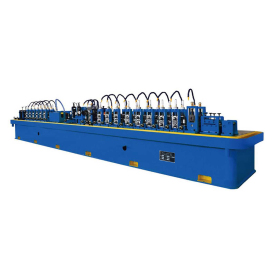
Exploring the Versatility and Efficiency of the All-in-One High Frequency Welder for Metal Fabrication Industries

Exploring the Versatility and Efficiency of the All-in-One High Frequency Welder for Metal Fabrication Industries
In conclusion, the all-in-one high frequency welder represents a significant leap forward in metal fabrication technology. Its versatility and efficiency are making waves across various industries, offering a comprehensive solution that meets the demands of modern welding applications. By amalgamating multiple welding processes into a single machine, fabricators can enhance productivity, reduce costs, and maintain high-quality standards in their work. As industries continue to seek innovations that improve their operations, embracing the capabilities of high frequency welders will undoubtedly prove to be a strategic choice for those involved in metal fabrication. The future holds great promise for businesses that leverage such advanced technology, setting the stage for more efficient and successful welding operations.