[Industrial tube making machinery]Exploring the Evolution and Significance of Industrial Tube Making Machinery in Modern Manufacturing Processes
News 2024-8-23
Industrial tube making machinery has played a critical role in the evolution of manufacturing processes across various sectors. As industries strive for efficiency and precision, the demand for high-quality tubes increases, leading to advancements in tube production technologies. This article delves into the historical development, types, applications, and future of industrial tube making machinery, highlighting its significance in contemporary manufacturing.
Historically, tube production has evolved significantly. The earliest methods of tube manufacturing involved rudimentary techniques that required significant manual labor and limited precision. However, with the advent of industrialization in the 19th century, machinery began to revolutionize production practices, making it faster and more efficient. Initially, methods such as drawing and welding were employed to produce tubes manually. Today, industrial tube making machinery encompasses sophisticated technologies that automate and enhance these processes, maximizing throughput and ensuring uniformity in product quality.
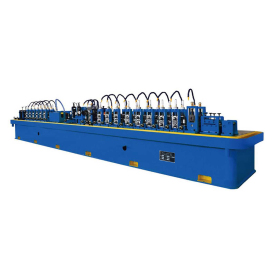
Exploring the Evolution and Significance of Industrial Tube Making Machinery in Modern Manufacturing Processes
The advancements in tube welding technology have also had a significant impact on industrial tube making machinery. High-frequency induction welding machines and laser welding technology have emerged as critical components in tube production, allowing for efficient and strong joints. These methods not only increase production speed but also improve the quality and reliability of the finished product. The integration of advanced methods such as robotic welding systems further enhances this process, ensuring precision and reducing human error.
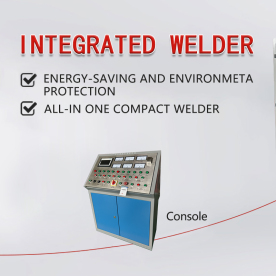
Exploring the Evolution and Significance of Industrial Tube Making Machinery in Modern Manufacturing Processes
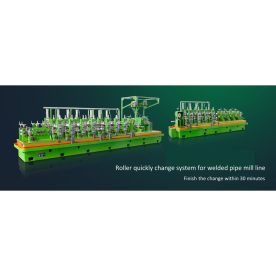
Exploring the Evolution and Significance of Industrial Tube Making Machinery in Modern Manufacturing Processes
As we look toward the future, the significance of industrial tube making machinery is poised to grow even more. Sustainable manufacturing practices are gaining traction, and machinery that minimizes waste while maximizing energy efficiency is likely to be a game-changer. Innovations such as additive manufacturing, or 3D printing of tubes, are slowly gaining ground, allowing for more complex geometries and tailored solutions.
In conclusion, industrial tube making machinery stands at the forefront of modern manufacturing processes, driving efficiency, quality, and innovation across diverse industries. As production demands continue to evolve, the machinery responsible for producing these vital components will also adapt, incorporating cutting-edge technologies that enhance performance and sustainability. Understanding the significance and applications of these machines not only underscores their importance in contemporary manufacturing but also highlights the endless possibilities that lie ahead in this dynamic field.