[Roller for tube mill]Understanding the Importance of Roller for Tube Mill in Modern Manufacturing Processes and How It Enhances Production Efficiency
News 2024-8-23
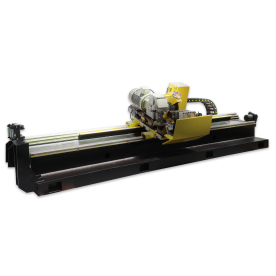
Understanding the Importance of Roller for Tube Mill in Modern Manufacturing Processes and How It Enhances Production Efficiency
The Role of Rollers in Tube Mills
Rollers are mechanical devices that are primarily responsible for shaping and forming the metal strips into tubes. These components facilitate the process of elongation and welding of the metallic material, leading to the formation of a round tube or pipe. The rollers guide the metal through various stages of the tube mill, ensuring precise dimensions and structural integrity.
In a typical tube mill, multiple rollers are arranged in a series, each with a specific purpose. Some rollers are designed for initial shaping, while others serve to refine the tube's dimensions and finalize the welding process. The arrangement and design of these rollers are crucial, as they must accommodate different thicknesses and widths of metal strips in a continuous flow without causing defects.
Design Considerations for Rollers
The design of rollers used in tube mills is critical for operational efficiency. Key considerations include:
1. **Material Selection**: Rollers must be made from high-quality materials that can withstand significant wear and tear. Common materials include hardened steel and specialized alloys designed to handle extreme conditions.
2. **Roller Geometry**: The shape of the rollers directly impacts the shaping of the tube. Designers take great care in defining the profile of each roller, optimizing it for the specific application. This geometry includes the diameter, width, and angle, affecting how the metal is formed as it passes through the rollers.
3. **Heat Treatment**: To enhance the longevity and durability of rollers, heat treatment processes like hardening are utilized. This process increases the surface hardness of the rollers, reducing wear and improving performance over time.
4. **Surface Finish**: The surface texture of rollers plays a crucial role in reducing friction and promoting smooth operation. A rough surface may lead to excessive wear and tear, while a very smooth finish may reduce the grip needed during the forming process.
Impact on Production Efficiency
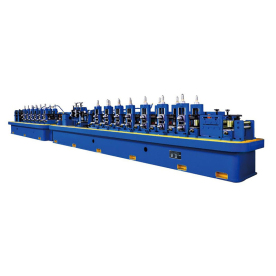
Understanding the Importance of Roller for Tube Mill in Modern Manufacturing Processes and How It Enhances Production Efficiency
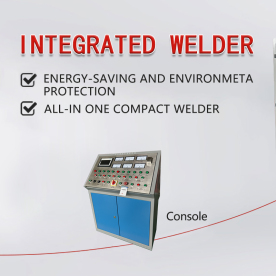
Understanding the Importance of Roller for Tube Mill in Modern Manufacturing Processes and How It Enhances Production Efficiency
2. **Reduced Downtime**: By optimizing roller design and maintenance schedules, manufacturers can reduce equipment downtime due to wear and malfunction. This leads to increased productivity as machinery remains in operation longer without interruptions.
3. **Improved Throughput**: The right rollers facilitate a smoother production process, allowing for higher speeds in the mill. This is particularly important in large-scale production environments where time is money.
4. **Energy Efficiency**: Well-designed rollers reduce friction and energy consumption during the tube forming process. This not only lowers operational costs but also contributes to a more environmentally sustainable manufacturing process.
Conclusion
In conclusion, rollers are a critical component of tube mills, impacting everything from the quality of the final product to the efficiency of the production process. As industries continue to evolve and demand higher precision and efficiency, the role of rollers becomes increasingly significant. Manufacturers must pay careful attention to the design and maintenance of these essential components to remain competitive in a fast-paced market.
As the manufacturing landscape develops, advancements in roller technology and material science will undoubtedly contribute to more efficient and effective tube mill operations, ensuring that this essential process meets the demands of modern industries. Understanding the intricacies of rollers for tube mills not only aids manufacturers in improving their productivity but also helps them achieve higher standards of quality and reliability in the products they deliver.