[Advanced Tube making machinery]The Evolution and Advantages of Advanced Tube Making Machinery in Modern Manufacturing Processes
News 2024-8-22
In today’s rapidly evolving manufacturing landscape, efficiency and productivity are paramount. Among the critical components that have transformed the manufacturing process is advanced tube making machinery. This sophisticated equipment has revolutionized how industries produce a variety of tube-related products, from simple metal pipes to complex, high-precision tubing for numerous applications.
Traditionally, tube making was a labor-intensive process, heavily reliant on manual operations and less efficient machines that often compromised on quality and precision. However, with the introduction of advanced tube making machinery, manufacturers can now achieve a new level of production efficiency, significantly reducing labor costs and improving product quality. These machines leverage cutting-edge technologies such as computer numeric control (CNC), high-speed production capabilities, and enhanced automation systems.
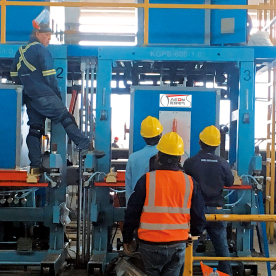
The Evolution and Advantages of Advanced Tube Making Machinery in Modern Manufacturing Processes
Moreover, advanced tube making machinery often incorporates automated systems that streamline the entire production process. By minimizing manual intervention, these machines significantly reduce the potential for human error, leading to higher consistency in quality. Additionally, automation allows for faster production cycles, meaning manufacturers can respond more swiftly to fluctuating market demands without compromising on quality or safety.
Energy efficiency is another significant advantage of modern tube making machinery. Traditional machinery often required substantial amounts of energy to operate, resulting in higher operational costs and a larger carbon footprint. In contrast, many advanced machines are designed to operate using less energy, aligning with global sustainability goals. Furthermore, these machines often feature innovative designs that minimize waste materials, further contributing to environmentally friendly manufacturing practices.
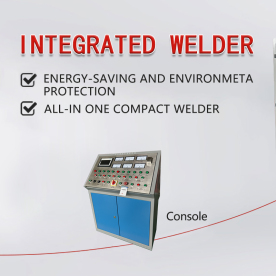
The Evolution and Advantages of Advanced Tube Making Machinery in Modern Manufacturing Processes
In the realm of research and development, advanced tube making machinery facilitates quicker prototyping and testing of new designs. Manufacturers can rapidly produce small batches of custom tubes to evaluate performance and identify potential improvements. This capability not only accelerates the innovation cycle but also empowers businesses to create tailored solutions for unique customer needs.
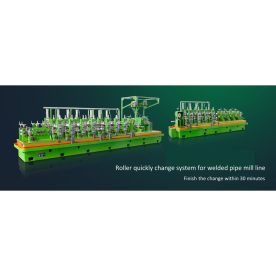
The Evolution and Advantages of Advanced Tube Making Machinery in Modern Manufacturing Processes
Furthermore, the digital transformation within the manufacturing sector has enabled the connectivity of advanced tube making machinery with broader systems, including supply chain management software and predictive maintenance tools. These connections provide manufacturers with real-time data about production efficiency, machine status, and overall workflow optimization. Implementing such sophisticated analytics allows businesses to make informed decisions that drive continuous improvements.
In conclusion, advanced tube making machinery represents a significant leap forward in manufacturing technology. By automating processes, improving precision, enhancing energy efficiency, and accommodating diverse materials, this machinery not only boosts productivity but also positions manufacturers to meet the demands of a challenging market. As industries continue to evolve, the role of advanced tube making machinery will undoubtedly be a cornerstone in shaping the future of manufacturing, presenting opportunities for innovation, sustainability, and competitiveness. Adopting such technologies will be essential for companies aiming to thrive in a landscape that increasingly values efficiency and sustainability.