[High frequency welder for plastic]Unlocking the Power of High Frequency Welders for Plastic: A Comprehensive Guide to Techniques, Applications, and Benefits
News 2024-8-22
High frequency welding for plastics has carved out a niche in the manufacturing world, providing a fast, efficient, and highly effective method for joining plastic materials. This state-of-the-art technology not only enhances the integrity of the finished products but also opens the door for innovative designs that were previously impractical or impossible using conventional welding techniques. This article explores the functions, applications, advantages, and key considerations of high frequency welders for plastic.
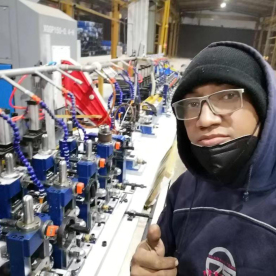
Unlocking the Power of High Frequency Welders for Plastic: A Comprehensive Guide to Techniques, Applications, and Benefits
High frequency welding, also known as dielectric welding or RF welding, utilizes electromagnetic energy to generate heat within the plastics being joined. Unlike traditional methods that apply heat from the outside or rely on friction, high frequency welding induces molecular friction at the interface of the materials. This allows thermoplastic materials to melt and bond at a molecular level, creating a strong and durable seam without the need for additional adhesives.
The high frequency welder itself is typically equipped with an oscillating generator that converts electrical energy into radio frequency energy, which is transmitted to the welding electrodes. The shape and configuration of the electrodes are crucial, as they directly influence the weld quality and depth of penetration.
Applications of High Frequency Welding
The versatility of high frequency welding makes it suitable for a wide range of industries and applications. Some of the most common include:
1. **Medical Devices and Supplies**: High frequency welding is widely used in the production of medical bags, pouches, and other disposable items. The process ensures a sterile seal, which is critical in healthcare settings.
2. **Automotive Components**: In the automotive industry, high frequency welders are employed to create durable components such as fuel tanks, air duct systems, and upholstery materials.
3. **Consumer Goods**: From inflatable products like toys and pool floats to technical textiles, high frequency welding allows for the efficient manufacture of consumer items that require reliable seals.
4. **Packaging**: The food and beverage industry benefits significantly from high frequency welding for packaging materials, ensuring a secure and hermetic seal that prolongs shelf life.
Advantages of High Frequency Welding
The use of high frequency welders for plastic offers numerous benefits that make it an attractive option for manufacturers:
- **Speed and Efficiency**: The process can produce welds in a matter of seconds, significantly reducing production times compared to traditional welding methods.
- **High Strength Joints**: The molecular bond created through high frequency welding is exceptionally strong, often exceeding the strength of the materials themselves.
- **Clean and Eco-Friendly**: Since the process does not require additional adhesives or chemicals, high frequency welding results in a cleaner workspace and minimizes environmental impact.
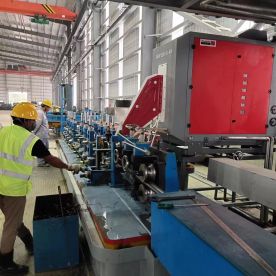
Unlocking the Power of High Frequency Welders for Plastic: A Comprehensive Guide to Techniques, Applications, and Benefits
- **Cost-Effectiveness**: With faster production times and less material waste, high frequency welding can be a cost-saving option in both the short and long term.
Key Considerations for Using High Frequency Welders
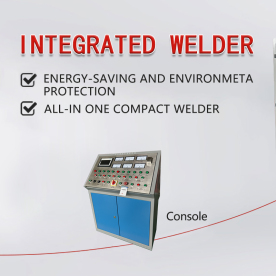
Unlocking the Power of High Frequency Welders for Plastic: A Comprehensive Guide to Techniques, Applications, and Benefits
- **Material Compatibility**: Not all plastics are suitable for high frequency welding. Generally, thermoplastics such as PVC, polyurethane, and certain types of nylon are ideal candidates, while thermosetting plastics may not work.
- **Equipment Investment**: High frequency welders can require a significant upfront investment, especially for high-capacity machines. Manufacturers should consider their production needs and potential return on investment before purchasing.
- **Technical Expertise**: Successfully using high frequency welders requires skilled operators who understand the nuances of the machinery and the materials being welded.
- **Testing and Quality Assurance**: Implementing a robust quality assurance process is essential to ensure the strength and durability of the welds, especially in critical applications like medical devices.
Conclusion
High frequency welders for plastic represent a cutting-edge manufacturing solution that combines speed, efficiency, and versatility. With their ability to create strong, reliable joints in a wide variety of applications, these machines have established themselves as an essential tool in numerous industries. Manufacturers looking to innovate and elevate their production processes should certainly consider the advantages of adopting high frequency welding as a core part of their operations. As technology continues to evolve, we can only expect the applications and efficiencies of high frequency welders to expand even further in the future.