[Industrial Solid state HF welder]Exploring the Advantages and Applications of Industrial Solid State HF Welders in Modern Manufacturing Processes
News 2024-8-22
In contemporary manufacturing environments, the need for efficient, high-quality welding solutions is more crucial than ever. Among the myriad of welding technologies available today, the Industrial Solid State HF Welder stands out as a game-changer in both performance and versatility. This welding method, distinguished by its use of high-frequency electrical currents and solid-state technology, is revolutionizing how manufacturers approach various material joining processes, offering numerous advantages that can enhance production quality and efficiency.
**Understanding Industrial Solid State HF Welding**
At its core, the Industrial Solid State HF Welder operates by generating high-frequency electromagnetic waves that induce heating within the workpieces. This method is particularly effective for welding materials such as plastics and metals, often used in the production of automotive parts, electronics, and packaging materials. The solid-state components in these welders, as opposed to traditional tube-based systems, provide a range of enhancements, including better reliability, increased energy efficiency, and reduced maintenance needs.
**Advantages of Industrial Solid State HF Welders**
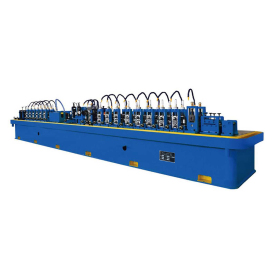
Exploring the Advantages and Applications of Industrial Solid State HF Welders in Modern Manufacturing Processes
2. **Enhanced Precision and Control**: Industrial Solid State HF Welders are renowned for their ability to provide precise control over the welding process. This precision allows manufacturers to achieve consistent weld quality with various materials and thicknesses. Advanced digital controls enable operators to fine-tune parameters such as power output and frequency, ensuring optimal welding conditions tailored to specific requirements.
3. **Minimal Maintenance**: Solid-state technology reduces the need for extensive maintenance typically associated with conventional high-frequency welders. With fewer moving parts and a robust design, these machines experience less wear and tear, decreasing downtime and repair costs. This reliability is a significant advantage in high-volume production environments where every minute counts.
4. **Versatile Applications**: The versatility of Industrial Solid State HF Welders is one of their most appealing traits. They can be used across various industries, including automotive, aerospace, electronics, and packaging. Whether it’s welding plastic components in automotive assemblies or creating seams in flexible packaging materials, these welders can adapt to multiple applications effortlessly.
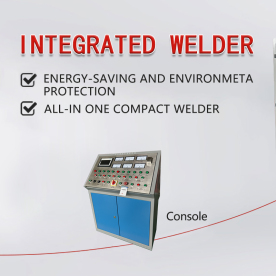
Exploring the Advantages and Applications of Industrial Solid State HF Welders in Modern Manufacturing Processes
6. **Rapid Production Times**: The quick setup and fast welding cycles of solid-state HF welders lead to increased production speed. As industries strive to meet tight deadlines and high product demand, the ability to weld faster without compromising quality is an invaluable asset.
**Applications Across Industries**
In the automotive sector, the Industrial Solid State HF Welder is extensively used for welding dashboard components, plastic housings, and electrical connections. The aerospace industry employs these welders for joining lightweight materials, achieving structural integrity while adhering to strict weight regulations. Additionally, in the electronics sector, solid-state HF welding is vital for assembling consumer gadgets, providing reliable connections that enhance product durability.
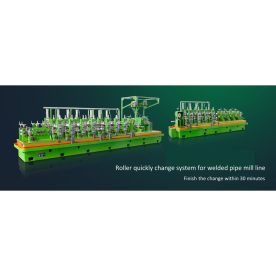
Exploring the Advantages and Applications of Industrial Solid State HF Welders in Modern Manufacturing Processes
**Conclusion**
As industries continue to evolve, the importance of advanced welding technologies like the Industrial Solid State HF Welder cannot be overstated. Their energy efficiency, precision, versatility, and minimal maintenance requirements make them ideal for modern manufacturing processes. As manufacturers look to enhance production capabilities while reducing environmental footprints, adopting solid-state HF welding technology may soon become not just a choice but a necessity for staying competitive in an increasingly demanding market. The future looks bright for this innovative welding method — a true testament to the potential of solid-state engineering in reshaping the manufacturing landscape.