[Complete Pipe mill production line solution]Comprehensive Overview of Complete Pipe Mill Production Line Solutions for Efficient Pipe Manufacturing
News 2024-8-22
****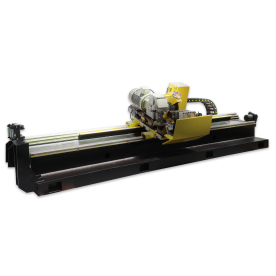
Comprehensive Overview of Complete Pipe Mill Production Line Solutions for Efficient Pipe Manufacturing
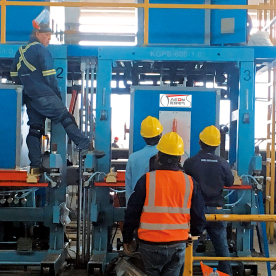
Comprehensive Overview of Complete Pipe Mill Production Line Solutions for Efficient Pipe Manufacturing
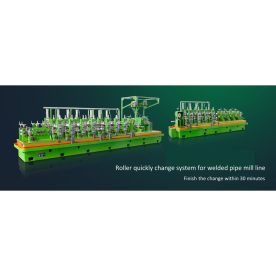
Comprehensive Overview of Complete Pipe Mill Production Line Solutions for Efficient Pipe Manufacturing
Key Components of a Complete Pipe Mill Production Line
1. **Raw Material Preparation**: The quality of the final product starts with the type and preparation of raw materials. A complete pipe mill utilizes advanced cutting, deburring, and cleaning systems to ensure that the raw materials are of the highest quality. Various types of strip steel or other materials are prepped to meet specified standards before they enter the production line.
2. **Forming Equipment**: Central to the pipe mill is the forming process, where raw material strips are shaped into pipes. This process typically involves roll forming or welding. Advanced technologies such as High Frequency Welding (HFW) or Submerged Arc Welding (SAW) are employed for creating strong seams, which enhance the integrity and durability of the final product.
3. **Sizing and Squaring**: After the pipes are formed, they must be sized accurately to meet customer specifications. The sizing section of the mill adjusts the dimensions of the pipes, ensuring uniformity and compliance with industry standards. Equipment like sizing stations and squaring units formulate pipes to precise specifications.
4. **Heat Treatment**: Certain pipe applications require enhanced mechanical properties. A complete pipe mill often integrates heat treatment processes such as normalization, annealing, or quenching. These processes not only improve the strength of the material but also reduce residual stresses that could affect the performance of the final product.
5. **Finishing and Coating**: Once the pipes have been formed and treated, finishing touches are applied. This may include surface treatments like grinding, polishing, or powder coating to achieve the desired aesthetic and functional properties of the pipes. Proper finishing also helps protect against corrosion, enhancing the longevity of the products.
6. **Inspection and Quality Control**: Quality assurance is fundamental in the pipe manufacturing process. A complete pipe mill production line implements advanced inspection technologies such as ultrasonic testing, eddy current testing, or X-ray inspection systems. These technologies ensure that any defects in the pipes are detected before they reach the market, safeguarding the manufacturer’s reputation.
7. **Packaging and Shipping**: The final stage of the production line involves packaging and preparing products for shipment. Automated packaging systems ensure that pipes are securely bundled and labeled according to specifications, ready for efficient transport to customers.
Advantages of a Complete Pipe Mill Production Line
The implementation of a complete pipe mill production line solution offers numerous advantages to manufacturers:
- **Increased Efficiency**: Automation and integrated processes eliminate bottlenecks and significantly reduce production time. This efficiency allows for increased order capacity without sacrificing quality.
- **Consistency and Quality**: With state-of-the-art technology and rigorous testing at every stage, manufacturers can ensure consistent quality in their products. This reliability is crucial for maintaining long-term relationships with customers.
- **Flexibility**: Modern pipe mills are designed to accommodate a wide variety of pipe sizes and specifications, allowing manufacturers to respond quickly to changing market demands and customer requirements.
- **Cost Savings**: By optimizing every aspect of the production process and reducing waste, companies can achieve significant cost savings, enhancing overall profitability.
- **Environmental Considerations**: Advanced pipe mills often adopt eco-friendly practices, reducing their carbon footprint and energy consumption, which is increasingly important in today’s industrial landscape.
In conclusion, investing in a complete pipe mill production line solution not only enhances operational efficiency but also improves product quality and market competitiveness. For manufacturers looking to thrive in a demanding industry, these modern systems represent the future of pipe production. As technology continues to evolve, we can expect even greater innovations to emerge, further transforming the pipe manufacturing landscape.