[Automatic ERW tube mill equipment]Comprehensive Guide to Automatic ERW Tube Mill Equipment: Enhancing Precision and Efficiency in Tube Production
News 2024-8-22
In the ever-evolving landscape of manufacturing, the demand for high-quality tube products continues to grow, necessitating the use of advanced machinery to meet production standards. Automatic ERW (Electric Resistance Welding) tube mill equipment has emerged as a pivotal solution for manufacturers looking to optimize their operations while ensuring precision, efficiency, and durability in their products. This article delves into the functionality, benefits, and technical specifications of Automatic ERW tube mill equipment, underlining its significance in the modern manufacturing sector.
Understanding Automatic ERW Tube Mill Equipment
Automatic ERW tube mill equipment is designed to produce welded tubes and pipes from coils of steel or other metals. The process begins with the uncoiling of the metal strip, which is then shaped into a cylindrical form through a series of rollers. After the edges of the strip are brought together, an electric resistance welding process is utilized to fuse the edges, creating a continuous tube. This method is not only efficient but also provides strong, reliable welds, making it an ideal choice for a variety of applications including construction, automotive, and energy sectors.
Key Features of Automatic ERW Tube Mill Equipment
1. **High Production Speed**: One of the standout features of Automatic ERW tube mill equipment is its capacity for high production speeds. These machines can produce tubes at a rate significantly higher than traditional methods, reducing production time and increasing output. This is particularly important in industries where demand fluctuates rapidly.
2. **Precision Engineering**: Automatic ERW tube mills are equipped with advanced control systems that ensure precise calibration of parameters throughout the production process. This level of precision is vital for achieving the consistent dimensions and tolerances required by modern engineering applications.
3. **Versatility**: The equipment can accommodate various materials, including mild steel, stainless steel, and specialty alloys. This versatility allows manufacturers to produce a range of products, from standard structural tubes to specialized applications, without the need for extensive modifications.
4. **Automation and Integration**: Modern Automatic ERW tube mills incorporate advanced automation technologies that streamline the production process. From feeding the raw materials to quality control checks, automation reduces human error and enhances consistency in product quality. Additionally, many machines are designed to integrate with existing manufacturing systems, providing seamless operation within a larger production line.
5. **Energy Efficiency**: With a growing emphasis on sustainability, manufacturers are seeking ways to reduce energy consumption. Automatic ERW tube mill equipment is designed with energy-efficient motors and systems that minimize waste, contributing to lower operational costs and a reduced carbon footprint.
Applications of Automatic ERW Tube Mill Equipment
The applicability of Automatic ERW tube mill equipment spans various industries:
- **Construction**: Welded tubes are essential in constructing frames, scaffolding, and other structural applications where strength and durability are paramount. - **Automotive**: The automotive industry uses ERW tubes for making exhaust systems, chassis, and other components that require lightweight yet strong materials.
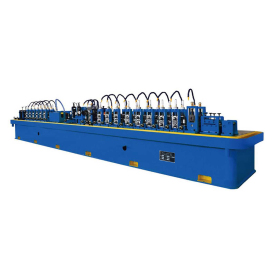
Comprehensive Guide to Automatic ERW Tube Mill Equipment: Enhancing Precision and Efficiency in Tube Production
Advantages Over Traditional Methods
Compared to traditional tube manufacturing methods, Automatic ERW tube mills offer numerous advantages, including:
- **Cost-Effectiveness**: The efficiency of automatic feeding and welding reduces labor costs and minimizes waste, leading to lower overall production costs.
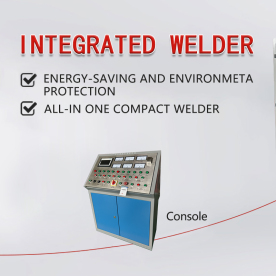
Comprehensive Guide to Automatic ERW Tube Mill Equipment: Enhancing Precision and Efficiency in Tube Production
- **Reduced Lead Times**: Faster production rates result in shorter lead times, allowing businesses to respond more quickly to market demands.
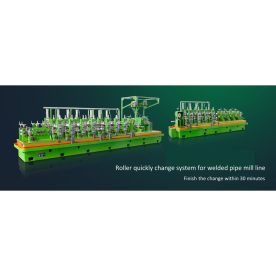
Comprehensive Guide to Automatic ERW Tube Mill Equipment: Enhancing Precision and Efficiency in Tube Production
As industries continue to evolve and the need for high-quality, versatile tube products increases, Automatic ERW tube mill equipment proves to be a vital asset for manufacturers. Its blend of high-speed production, precision engineering, and energy efficiency makes it a preferable choice for those seeking to enhance their competitive edge. Investing in this technology not only leads to operational improvements but also positions businesses to meet the future demands of manufacturing. As technology progresses, it is likely that we will see even further advancements in ERW tube mill capabilities, paving the way for even more efficient production processes.