[Customized ERW tube mill solutions]Innovative Customized ERW Tube Mill Solutions: Enhancing Efficiency and Versatility in Tube Production for Diverse Industries
News 2024-8-20
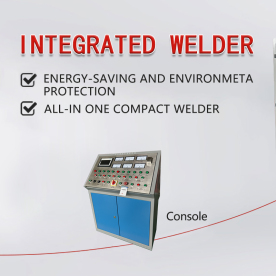
Innovative Customized ERW Tube Mill Solutions: Enhancing Efficiency and Versatility in Tube Production for Diverse Industries
ERW (Electric Resistance Welding) tube mills are pivotal in producing high-quality steel tubes utilized across numerous applications. These mills use a specialized welding process to join edges of metal strips, creating a continuous tube. Customized ERW tube mill solutions cater to the unique needs of manufacturers, allowing them to adapt machinery specifications based on the type of tube, material, and desired finish. This flexibility ultimately leads to improved productivity, reduced operational costs, and enhanced product performance.
Understanding the Core of ERW Technology
At the heart of ERW technology is the principle of resistance welding. High-frequency electrical currents are passed through the edges of the metal strip, heating the material to a plastic state, which facilitates the joining process. This method is highly efficient and produces strong, durable seams that withstand tensile and torsional forces.
As industries evolve, so do the requirements for tube production. Manufacturers often encounter challenges related to varying specifications, including size, wall thickness, surface finish, and alloy grades. Customized ERW tube mill solutions provide an effective response to these challenges by allowing modifications to machinery and processes that align with specific production goals.
Benefits of Customized ERW Tube Mill Solutions
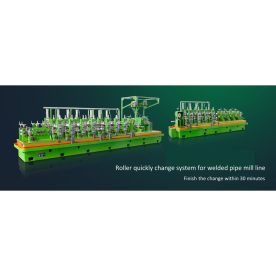
Innovative Customized ERW Tube Mill Solutions: Enhancing Efficiency and Versatility in Tube Production for Diverse Industries
2. **Enhanced Efficiency**: Customized solutions can significantly enhance productivity in manufacturing processes. By designing mills that streamline operations, reduce waste, and enable rapid setup changes, manufacturers can optimize their production lines. High-speed ERW mills, when combined with automation technology, can produce tubes at high throughput rates, thereby minimizing labor costs and lead times.
3. **Improved Quality Control**: Quality assurance is pivotal in tube production, especially when dealing with critical applications like structural tubing or oil pipelines. Customized ERW solutions incorporate advanced inspection systems and quality control measures, ensuring that each product meets stringent industry standards. This level of precision minimizes defects and rework, ultimately contributing to better performance and customer satisfaction.

Innovative Customized ERW Tube Mill Solutions: Enhancing Efficiency and Versatility in Tube Production for Diverse Industries
5. **Scalable Production**: As market demands fluctuate, the scalability of customized ERW tube mills ensures that manufacturers can quickly adapt without significant overhauls. This scalability is crucial for businesses looking to expand their product lines or enter new markets. With customized solutions, manufacturers can scale operations up or down in response to changing customer demands.
Industries Benefiting from Customized ERW Tube Mills
Various sectors rely heavily on customized ERW tube mill solutions, transforming their production capabilities. The automotive industry, for instance, uses specialized tubing for chassis components, exhaust systems, and fuel lines, demanding precision and reliability. In construction, ERW tubes are integral for scaffolding, framing, and piping applications, where structural integrity is non-negotiable.
Furthermore, the oil and gas industry requires robust and corrosion-resistant tubes for drilling and extraction processes. Customized solutions enable these manufacturers to produce tubes that can withstand harsh environmental conditions while maintaining high standards of safety and operational efficiency.
Conclusion
Customized ERW tube mill solutions are essential for modern manufacturers seeking to enhance productivity, quality, and adaptability. As industries continue to evolve, the ability to tailor production processes to meet specific needs will remain a critical factor for success. By embracing these innovative solutions, manufacturers can not only stay competitive but also pave the way for future advancements in tube production technologies. With enhanced flexibility, efficiency, and quality control, the advantages of customized ERW tube mills are clear, and their significance in the manufacturing landscape will only grow.