[Energy-efficient Pipe mill production line]Transforming Manufacturing: The Role of Energy-efficient Pipe Mill Production Line in Sustainable Industry Practices
News 2024-8-20
****In recent years, the push for sustainability and energy efficiency has permeated various sectors, fundamentally altering production processes. One of the critical areas where these changes are taking root is in the manufacturing of pipes. The advent of the energy-efficient pipe mill production line marks a pivotal shift in how pipes are produced, leading to decreased energy consumption, lower emissions, and cost savings. As industries face increasing pressures to reduce their carbon footprints and comply with environmental standards, the need for energy-efficient production methods has never been more pressing.
Energy-efficient pipe mill production lines utilize advanced technologies and innovative practices that significantly reduce the energy consumption associated with pipe manufacturing. Traditional pipe mills often rely on old technologies and techniques that consume vast amounts of energy, contributing to increased operational costs and environmental degradation. However, the modern energy-efficient pipe mill production line incorporates a variety of cutting-edge technologies aimed at optimizing energy usage without compromising quality or output.
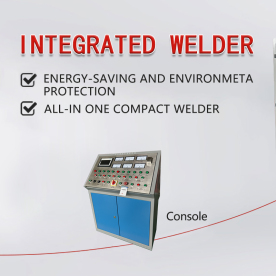
Transforming Manufacturing: The Role of Energy-efficient Pipe Mill Production Line in Sustainable Industry Practices
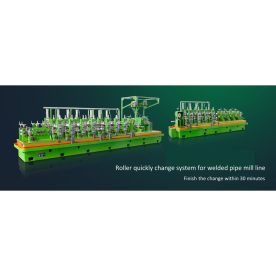
Transforming Manufacturing: The Role of Energy-efficient Pipe Mill Production Line in Sustainable Industry Practices

Transforming Manufacturing: The Role of Energy-efficient Pipe Mill Production Line in Sustainable Industry Practices
The materials used in the pipe manufacturing process have also evolved, with a growing trend towards using recycled or more sustainable raw materials. Energy-efficient pipe mills often source materials that require less energy to process. For example, the use of lightweight metals and composite materials can significantly reduce the energy required during the forming and welding processes. Additionally, these sustainable materials can enhance the overall performance and durability of pipes, leading to longer lifetimes and reduced need for replacements.
Moreover, energy-efficient pipe mill production lines are designed with efficiency in mind throughout the entire production process. From the initial stages of material preparation to the final quality control checks, every phase is subjected to rigorous analysis and optimization. For example, advanced welding techniques, such as laser welding, promote stronger and more precise joins, thereby reducing the energy expended during the manufacturing process. These welding techniques are more efficient than traditional methods, investing less energy while providing enhanced durability.
The benefits of adopting energy-efficient pipe mill production lines extend beyond mere energy savings. These advancements can improve product quality, enhance operational efficiency, and reduce waste, all of which translate into significant cost savings over time. Manufacturers can pass these savings on to customers, potentially leading to competitive pricing in the market. Furthermore, companies that invest in energy-efficient technologies often see enhanced brand reputation, as they align themselves with the growing consumer demand for environmentally responsible products and practices.
Lastly, compliance with regulatory standards is another compelling reason for the shift toward energy-efficient pipe mill production lines. Many regions are implementing stricter environmental regulations aimed at reducing industrial emissions and promoting sustainable practices. By adopting energy-efficient technologies, manufacturers can stay ahead of these regulations, avoiding potential fines and fostering positive relationships with stakeholders, including the government and local communities.
In conclusion, energy-efficient pipe mill production lines represent a crucial evolution in the manufacturing industry, embodying the integration of sustainability into daily operations. The combination of advanced technologies, innovative practices, and the pursuit of higher efficiency sets a new standard in pipe production. As industries gear up for a greener future, the implementation of energy-efficient production lines will play a vital role in achieving a balanced approach to profitability, environmental responsibility, and operational excellence.