[High-efficiency pipe mill production line]Maximizing Output and Reducing Waste with a High-Efficiency Pipe Mill Production Line: The Future of Pipeline Manufacturing
News 2024-8-20
In the ever-evolving world of manufacturing, efficiency and waste reduction stand as vital goals for companies striving to remain competitive. The high-efficiency pipe mill production line, designed specifically for the production of pipes, plays a significant role in meeting these challenges head-on. Through cutting-edge technology and innovative designs, these production lines not only increase output but also enhance product quality and minimize resource consumption.
Historically, pipe manufacturing relied on labor-intensive processes and limited technology, resulting in high production costs and significant waste. However, advancements in machinery and production techniques have transformed this landscape, making the high-efficiency pipe mill the centerpiece of modern pipe manufacturing. These production lines are engineered to operate continuously, streamlining each step of the pipe creation process from raw material handling to final product output.
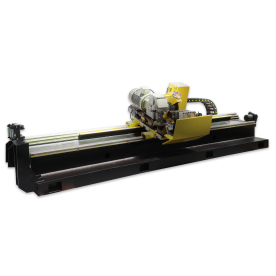
Maximizing Output and Reducing Waste with a High-Efficiency Pipe Mill Production Line: The Future of Pipeline Manufacturing
One of the most significant advantages of high-efficiency pipe mills is their ability to produce a wide range of pipe sizes and materials. This flexibility allows manufacturers to respond quickly to market demands and tailor their offerings to customer specifications without sacrificing efficiency. High-speed welding technologies, often employed in these production lines, enable the seamless joining of pipe segments at unprecedented speeds, ensuring that manufacturers can meet tighter deadlines and tighter budgets.
Moreover, these advanced production lines incorporate methods for real-time quality monitoring. Sensors and advanced analytics software monitor various parameters such as temperature, pressure, and tensile strength during the production process. By continuously assessing product quality, manufacturers can identify and rectify discrepancies before they escalate into costly failures. This not only enhances the quality of the final product but also reduces the amount of scrap generated during manufacturing—a key metric in assessing efficiency.
Environmental sustainability is another vital consideration that drives the adoption of high-efficiency pipe mill production lines. With growing concerns around climate change and resource depletion, manufacturers are increasingly seeking ways to operate sustainably. High-efficiency production lines consume less energy and water and produce lower emissions compared to traditional manufacturing methods. Furthermore, by producing less scrap and waste, companies can contribute to a circular economy. This sustainable approach not only appeals to environmentally conscious consumers but often aligns with governmental regulations aimed at reducing industrial impact.
Investment in advanced technologies, such as high-efficiency pipe mill production lines, is also key to future-proofing manufacturing businesses. The pipe industry faces the pressures of fluctuating raw material prices and stringent regulatory requirements. Companies that embrace high-efficiency production systems can better weather these challenges, ensuring greater long-term stability and profitability.
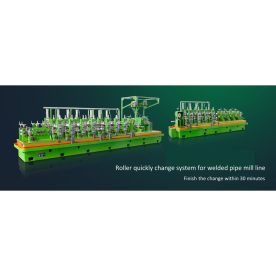
Maximizing Output and Reducing Waste with a High-Efficiency Pipe Mill Production Line: The Future of Pipeline Manufacturing
