[Industrial All-in-one High Frequency Welder]Understanding the Benefits and Applications of Industrial All-in-One High Frequency Welders for Modern Manufacturing
News 2024-8-20
****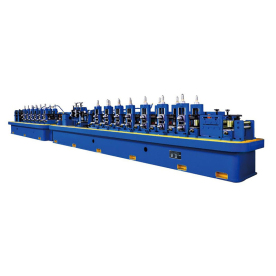
Understanding the Benefits and Applications of Industrial All-in-One High Frequency Welders for Modern Manufacturing
What is an Industrial All-in-One High Frequency Welder?
An industrial all-in-one high frequency welder is a sophisticated welding machine that utilizes high-frequency electric currents to establish a bond between materials. Unlike traditional welding processes that rely solely on heat to fuse metals, high frequency welding employs electromagnetic fields to bring the components together, resulting in a strong and durable joint. These machines are often equipped with advanced features such as adjustable power settings, digital controls, and compatibility with various materials including plastics, metals, and composites. The all-in-one design allows for different welding processes, such as RF (radio frequency) welding, ultrasonic welding, and induction heating, all within a single framework.
Advantages of All-in-One High Frequency Welders
1. **Versatility**: One of the most significant advantages of an industrial all-in-one high frequency welder is its versatility. These machines can handle a wide range of materials and manufacturing processes, allowing businesses to use a single piece of equipment for multiple applications. This reduces the need for investing in several machines, thus saving space and operational costs.
2. **Efficiency**: High frequency welding is known for its quick processing times. The use of electromagnetic fields accelerates the melting and joining of materials, leading to shorter production cycles. This efficiency not only increases output but also improves overall productivity in manufacturing processes.
3. **Quality of Welds**: The precision offered by high frequency welding ensures strong and consistent welds. This is particularly advantageous when working with sensitive materials, where traditional welding methods might compromise integrity. High frequency welders reduce the risk of defects, leading to higher quality end products.
4. **Energy Savings**: All-in-one systems are designed for energy efficiency. They consume less power compared to conventional welding machines, which can result in significant cost savings over time. This feature makes them an environmentally friendly option for manufacturers looking to reduce their carbon footprint.
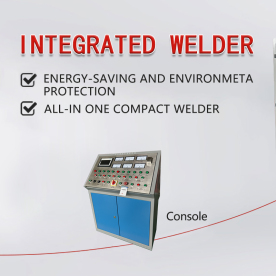
Understanding the Benefits and Applications of Industrial All-in-One High Frequency Welders for Modern Manufacturing
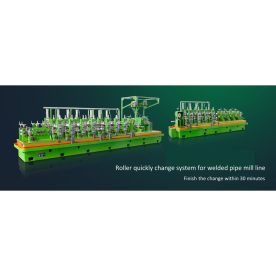
Understanding the Benefits and Applications of Industrial All-in-One High Frequency Welders for Modern Manufacturing
Industrial all-in-one high frequency welders find applications across various sectors, demonstrating their adaptability and utility.
- **Textiles and Apparel**: These machines are commonly used in the textile industry for bonding synthetic fabrics, seams, and hems without stitching. They allow for waterproof seams and produce aesthetically pleasing finishes.
- **Packaging**: In the packaging industry, high frequency welding is ideal for creating heat-sealed packaging solutions. This process maintains the integrity of food products while reducing the risk of contamination.
- **Automotive Manufacturing**: The automotive sector benefits from high frequency welders for the assembly of components such as dashboards and seat covers, where strong and durable joints are crucial.
- **Medical Devices**: High frequency welding is critical in the manufacture of medical devices, where sanitary conditions are essential. The process creates strong, well-sealed components that meet strict industry standards.
- **Construction and Building Materials**: These welders are also utilized in the construction industry for various applications, including the fabrication of composite materials and insulation products.
Conclusion
As industrial needs evolve, the demand for efficient, reliable, and versatile welding solutions continues to grow. Industrial all-in-one high frequency welders have proven to be a game-changer in the manufacturing landscape. Their numerous benefits, including versatility, efficiency, and superior quality of welds, make them an invaluable asset for companies striving to enhance their production capabilities. By adopting this advanced technology, manufacturers can ensure they remain competitive in an ever-changing market. As more industries recognize the advantages offered by all-in-one high frequency welders, we can expect to see their adoption becoming increasingly widespread in the years to come.