[Roller for tube mill]Understanding the Role of Rollers in Tube Mill Operations: Key Benefits, Types, and Maintenance Strategies
News 2024-8-16
When it comes to tube mill operations, the importance of rollers cannot be understated. These mechanical components not only facilitate the manufacturing process of tubes but also enhance the overall efficiency and productivity of the mill. In this article, we will explore the various types of rollers used in tube mills, their vital functions, advantages, and essential maintenance strategies to ensure optimal performance.
The Importance of Rollers in Tube Mills
Rollers are crucial to the functioning of a tube mill. They are primarily responsible for shaping, sizing, and finishing the tubes produced by the mill. The process begins with the feeding of flat metal strips into the mill, where rollers subject the metal to a series of bending and forming processes, gradually shaping it into a tube. The precise alignment and adjustment of these rollers are vital for producing tubes that meet stringent specifications in terms of diameter, wall thickness, and surface finish.
Types of Rollers Used in Tube Mills
There are several types of rollers utilized in tube mills, each designed to perform specific tasks throughout the manufacturing process:
1. **Forming Rollers**: These rollers are primarily responsible for shaping the flat metal strips into cylindrical forms. They come in various geometric shapes and configurations to accommodate different tube dimensions.
2. **Sizing Rollers**: Once the tube has been formed, sizing rollers come into play. Their job is to ensure that the tube meets the required dimensions and tolerances. These rollers apply pressure on the tube to achieve the desired diameter and wall thickness.
3. **Finishing Rollers**: After sizing, finishing rollers smooth out the tube’s surface, removing any imperfections and ensuring a refined finish. This step is crucial for applications where aesthetic appearance or smoothness is essential.
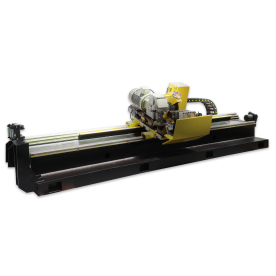
Understanding the Role of Rollers in Tube Mill Operations: Key Benefits, Types, and Maintenance Strategies
Advantages of Using High-Quality Rollers
Investing in high-quality rollers for tube mills can yield numerous benefits, including:
1. **Improved Productivity**: High-quality rollers enhance the efficiency of the tube formation process, reducing waste and increasing the throughput of the mill.
2. **Consistent Quality**: With precise engineering and construction, high-quality rollers ensure that the tubes produced meet stringent quality standards, which is crucial for applications in industries such as construction, automotive, and manufacturing.
3. **Reduced Maintenance Costs**: Durable rollers require less frequent replacement and maintenance, saving mill operators time and money in the long run.
4. **Enhanced Performance**: High-quality rollers can withstand high levels of stress and wear, ensuring consistent performance under various operating conditions.
Maintenance Strategies for Rollers in Tube Mills
To ensure the longevity and optimal performance of rollers in tube mills, it is imperative to establish a comprehensive maintenance program. Here are some essential strategies:
1. **Regular Inspections**: Conduct routine inspections of rollers to identify any signs of wear, misalignment, or damage. Early detection of issues can prevent more significant problems down the line.
2. **Lubrication**: Proper lubrication is essential to reduce friction and wear between rollers. Use high-quality lubricants and adhere to a regular lubrication schedule to keep rollers in peak condition.
3. **Alignment Checks**: Regularly checking and adjusting the alignment of rollers is crucial. Misalignment can lead to uneven wear, operational inefficiencies, and ultimately product defects.
4. **Cleaning**: Accumulation of debris and oxidation can affect the performance of rollers. Regularly clean the rollers to remove contaminants and maintain their integrity.
5. **Replacement of Worn-Out Rollers**: Keeping track of roller wear and replacing them as necessary is crucial for maintaining mill efficiency. Establish a wear limit and proactively replace rollers before they reach this threshold.
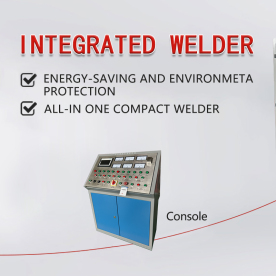
Understanding the Role of Rollers in Tube Mill Operations: Key Benefits, Types, and Maintenance Strategies
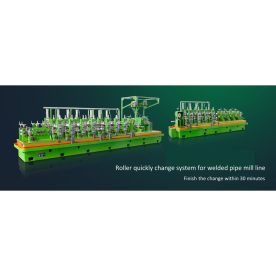