[Replacement Moulds for Tube Mills]Exploring the Advantages of Utilizing Replacement Moulds for Tube Mills: Enhancing Efficiency and Reducing Downtime in Manufacturing
News 2024-8-15
****In the modern manufacturing landscape, industries continuously strive for efficiency, cost-effectiveness, and optimal output. Tube mills, essential for processing and manufacturing various types of tubular products, often rely on precise moulds to shape their output. However, as production demands increase and technological advancements evolve, the need for replacement moulds for tube mills has come to the forefront. This article delves into the significance of replacement moulds and their advantages in enhancing efficiency and reducing downtime in manufacturing processes.
Understanding Tube Mills and Their Function
Tube mills are an integral component of many manufacturing sectors, including construction, automotive, and consumer goods. They utilize a continuous process to produce tubular products by rolling and welding steel strips or sheets into various shapes and sizes. Employing high-quality moulds is crucial for ensuring the integrity and precision of these products. However, like any mechanical component, these moulds wear down over time, necessitating timely replacements to maintain production standards.
The Importance of Replacement Moulds for Tube Mills
1. **Minimized Downtime**: One of the most significant benefits of using replacement moulds is the reduction in downtime. Production can be halted when moulds in use become worn or damaged, leading to costly downtime. By having a set of replacement moulds readily available, manufacturers can quickly swap out the old moulds for new ones, ensuring that production can continue with minimal interruptions.
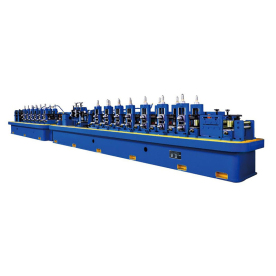
Exploring the Advantages of Utilizing Replacement Moulds for Tube Mills: Enhancing Efficiency and Reducing Downtime in Manufacturing
3. **Cost-Effectiveness**: While investing in replacement moulds may seem like an additional expense, the long-term savings resulting from reduced downtime, improved product quality, and fewer defects often outweigh this initial cost. Furthermore, replacement moulds can also lead to increased operational efficiency, allowing manufacturers to produce more units within a given timeframe, ultimately boosting revenue.
4. **Adaptability to New Technologies**: As manufacturing techniques and technologies advance, so do the requirements for the moulds used in tube mills. Replacement moulds provide manufacturers the flexibility to adapt to new processes or materials that may arise in the industry. This adaptability ensures that production methods are kept up-to-date, allowing companies to stay competitive in the market.
5. **Tailored Solutions**: Replacement moulds can be custom-designed to meet specific production needs. This flexibility allows manufacturers to readily adapt their output to changing market demands or client specifications. Custom moulds cater to unique designs and dimensions, enabling manufacturers to diversify their product offerings and tap into new market opportunities.
The Processes Involved in Sourcing Replacement Moulds
Sourcing replacement moulds for tube mills involves several critical steps:
- **Assessment**: Regular assessment of existing moulds is essential to determine wear and required replacement timelines. Implementing a robust maintenance schedule can aid in identifying potential issues before they escalate.
- **Vendor Selection**: Choosing a reliable supplier is vital for ensuring the quality of replacement moulds. Manufacturers should look for vendors with a strong reputation in the industry, capable of providing high-quality products and services.
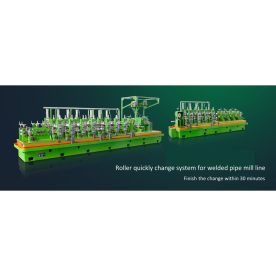
Exploring the Advantages of Utilizing Replacement Moulds for Tube Mills: Enhancing Efficiency and Reducing Downtime in Manufacturing
- **Training and Installation**: Proper installation and familiarity with new moulds are crucial to maximize their benefits. Training employees to handle and install replacement moulds can further streamline the transition process and ensure efficiency.
Conclusion
