[High frequency welder for plastic]Exploring the Advancements and Applications of High-Frequency Welder for Plastic in Modern Manufacturing Processes
News 2024-8-14
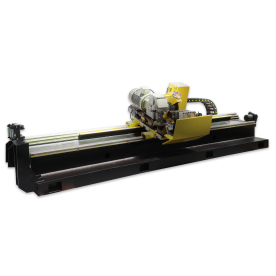
Exploring the Advancements and Applications of High-Frequency Welder for Plastic in Modern Manufacturing Processes
In today's rapidly progressing world of manufacturing, the need for innovative and efficient processes has never been more critical. Among these advancements, high-frequency welding technology has emerged as a superior method, particularly when it comes to welding plastics. High-frequency welders for plastic are revolutionizing industries that rely heavily on plastic products, including automotive, medical, and consumer goods. This article delves into the principles, advantages, and applications of high-frequency welders, illuminating their pivotal role in the manufacturing landscape.
Understanding High-Frequency Welding
High-frequency welding, also known as radio frequency (RF) welding, is a process that utilizes electromagnetic energy to generate heat in the plastic being joined. The core principle behind this welding method lies in the dielectric properties of thermoplastics, which absorb the high-frequency electromagnetic energy. When subjected to this energy, the materials' molecules vibrate, resulting in an increase in temperature that ultimately leads to melting and fusion of the plastic surfaces being joined.
This method is particularly effective for materials such as PVC, EVA, and certain types of polyurethane. The ability to use high-frequency welders for plastic is due to the unique characteristics of these materials, which respond favorably to electromagnetic energy, allowing for clean and efficient welding.
Advantages of High-Frequency Welders for Plastic
**1. Speed and Efficiency:** One of the most significant advantages of high-frequency welders is their speed. This welding method produces a bond in a matter of seconds, greatly enhancing productivity. Traditional welding processes can take much longer and may require extensive post-processing, which can slow down manufacturing lines.
**2. Strong and Durable Joints:** High-frequency welding creates exceptionally strong bonds that are often stronger than the original material. This quality is crucial in industries where durability is a must, such as automotive and aerospace manufacturing.
**3. Minimal Material Distortion:** Because the heating occurs only at the welding interface, high-frequency welding minimizes the risk of warping or weakening adjacent areas of the material. This feature is particularly valuable when working with complex shapes and designs.
**4. Versatility:** High-frequency welders for plastic can be adapted to accommodate a wide range of plastic types and thicknesses. This versatility makes them a preferred choice for manufacturers dealing with various plastic components.
**5. Environmentally Friendly:** Unlike traditional welding methods that may require adhesives or solvents, high-frequency welding is a clean process that does not introduce harmful substances into the environment. The elimination of chemicals is beneficial from both a regulatory and sustainability standpoint.
Applications of High-Frequency Welding in Industry
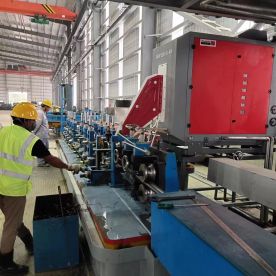
Exploring the Advancements and Applications of High-Frequency Welder for Plastic in Modern Manufacturing Processes
**1. Automotive Manufacturing:** In the automotive industry, high-frequency welding is used to create strong joints in components such as dashboards, seat covers, and airbag systems. The speed and reliability of this process significantly contribute to the production efficiency and safety of modern vehicles.
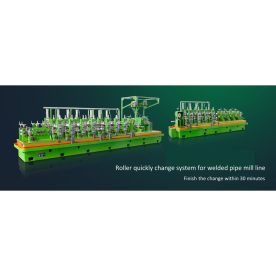
Exploring the Advancements and Applications of High-Frequency Welder for Plastic in Modern Manufacturing Processes
**3. Consumer Products:** High-frequency welding is prevalent in the manufacturing of consumer goods, such as inflatable products, protective covers, and packaging. The efficiency and strength of the welds produced enhance both the functionality and aesthetic appeal of these products.
**4. Textile Industry:** In textiles, high-frequency welding is employed to bond synthetic fabrics, enabling the creation of waterproof seams in garments and outdoor gear. This technology allows for innovative designs while maintaining product integrity.
**5. Solar Energy Applications:** High-frequency welding is increasingly used in the production of photovoltaic panels, where it facilitates the joining of various plastic components, such as back sheets and junction boxes.
Conclusion
The high-frequency welder for plastic is transforming the way manufacturers approach the creation of plastic components across various industries. Its combination of speed, strength, and environmental friendliness makes it an invaluable tool in modern production processes. As technology continues to advance, the scope of applications for high-frequency welding is likely to expand, solidifying its position as a cornerstone of efficient, innovative manufacturing. As industries evolve, embracing such technologies will be key to maintaining a competitive edge and meeting the ever-growing demands of the global market.