[Shear&butt welder]Understanding the Role of Shear & Butt Welders in Modern Fabrication Techniques: Enhancing Strength and Precision in Welding Applications
News 2024-8-14
The world of manufacturing and fabrication is constantly evolving, driven by the need for stronger, more efficient, and reliable products. One of the key components in this industry is welding – a technique used to join materials, primarily metals, to create robust structures. Among the various welding methods available, shear and butt welding have gained prominence due to their unique capabilities and applications. This article will explore the intricacies of shear and butt welders, their operational mechanics, and their importance in contemporary fabrication practices.
**What Is Shear & Butt Welding?**
Shear and butt welding are specific welding techniques that involve the joining of two metal pieces, typically along their edges. The term "butt welding" refers to a process where two workpieces are placed edge-to-edge and melted together, creating a seamless bond. Widely used in industries such as automotive, aerospace, and construction, butt welds are known for their strength and ability to produce a smooth finish on the joint.
On the other hand, shear welding encompasses a method where metal pieces are subjected to shear forces before being joined. This technique is beneficial in applications where the alignment and positioning of the components are critical. By applying pressure to the edges of the workpieces, shear welders can create a joint that can withstand significant stress and strain.
**The Mechanics of Shear & Butt Welders**
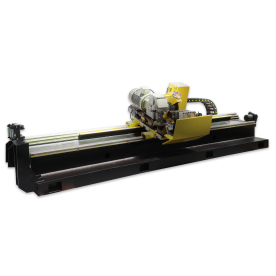
Understanding the Role of Shear & Butt Welders in Modern Fabrication Techniques: Enhancing Strength and Precision in Welding Applications
Both methods have their advantages, including the ability to weld dissimilar materials, reduced cycle times, and minimized distortion of the welded pieces. The selection of the appropriate welding technique depends on the materials in question, the specific application, and the required properties of the final weld.
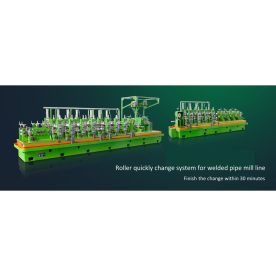
Understanding the Role of Shear & Butt Welders in Modern Fabrication Techniques: Enhancing Strength and Precision in Welding Applications
Shear and butt welding find applications in numerous industries and sectors. In the automotive industry, these methods are employed to fabricate chassis components, exhaust systems, and body panels where strength and weight reduction are critical factors. The aerospace sector benefits from these welding techniques in the assembly of aircraft structures, where precision and durability are of utmost importance.
In the realm of civil engineering, shear and butt welders are used in the construction of bridges, pipelines, and other infrastructure projects that demand high-strength joints capable of enduring significant loads and environmental stressors. The use of butt welding in the fabrication of high-pressure pipes, for instance, ensures leak-proof systems essential for oil and gas transport.
**Advantages of Using Shear & Butt Welders**

Understanding the Role of Shear & Butt Welders in Modern Fabrication Techniques: Enhancing Strength and Precision in Welding Applications
Second, these welding methods facilitate the joining of dissimilar materials, making it easier for manufacturers to innovate and develop complex assemblies. This capability is crucial in advanced manufacturing processes, where new material combinations can enhance performance and reduce overall weight.
Moreover, the efficiency of shear and butt welding contributes to reduced production times and lower operational costs. The ability to achieve strong and durable joints quickly minimizes the need for additional finishing work, which can further enhance the productivity of manufacturing workflows.
**Conclusion**
Shear and butt welders play an integral role in modern fabrication, offering remarkable strength and precision to welded joints across various industries. The evolution of welding technologies continues to drive improvements in manufacturing capabilities, enabling the production of more complex and advanced products. As industries strive for greater efficiency and sustainability, the importance of shear and butt welding techniques will undoubtedly continue to grow, solidifying their place in the future of engineering and fabrication.