[Industrial-grade induction heating equipment]Exploring the Advantages and Applications of Industrial-Grade Induction Heating Equipment in Modern Manufacturing Processes
News 2024-8-13
****Induction heating technology has revolutionized the way industrial heating tasks are executed, offering efficient and precise heating solutions tailored for various applications. Industrial-grade induction heating equipment stands out in numerous sectors, including automotive, aerospace, metal processing, and more, due to its unmatched efficiency, accuracy, and safety features. This article delves into the advantages these systems bring to modern manufacturing processes, their applications, and considerations for implementing them in different industries.
Understanding Induction Heating Technology
Induction heating operates on the principle of electromagnetic induction, where an electric current is passed through a coil, generating a magnetic field. When a conductive material, such as metal, is introduced into this magnetic field, it induces electric currents (eddy currents) within the material. These currents generate heat due to the electrical resistance of the material. This process allows for rapid and uniform heating, as opposed to conventional methods that often involve direct flames or resistive heating elements.
Advantages of Industrial-Grade Induction Heating Equipment
1. **Efficiency and Speed**: One of the most significant advantages of industrial-grade induction heating equipment is its efficiency. The ability to heat materials rapidly and uniformly translates into significant time savings in production cycles. Furthermore, induction heating systems generally consume less energy than traditional heating methods, making them both cost-effective and environmentally friendly.
2. **Precision Control**: These systems allow for precise temperature control, which is paramount in applications requiring accurate heat treatment. Operators can set specific temperature thresholds and monitor the heating process in real-time. This precision helps ensure consistent quality in finished products and reduces waste caused by overheating or underheating.
3. **Safety Improvements**: Unlike traditional heating methods that may expose operators to high flames or heated surfaces, induction heating equipment is inherently safer. The heat is generated within the material itself rather than on an external surface, which minimizes the risks of burns and workplace accidents. Additionally, many modern systems come equipped with safety features that automatically shut down operations in case of malfunctions.
4. **Versatility**: Industrial-grade induction heating equipment can be used for a wide range of applications, from melting metal and hardening surfaces to brazing and soldering components. Its adaptability makes it suitable for various manufacturing sectors, including electronics, automotive, and aerospace engineering.
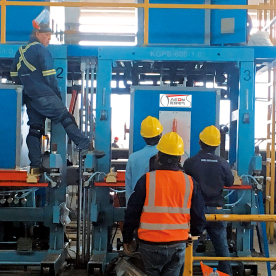
Exploring the Advantages and Applications of Industrial-Grade Induction Heating Equipment in Modern Manufacturing Processes
Applications of Industrial-Grade Induction Heating Equipment
1. **Metal Hardening**: In the automotive and aerospace industries, components like gears, shafts, and bearings often undergo hardening treatments to increase their lifespan and performance. Induction heating is highly effective for hardening process due to its rapid heating capabilities and precision.
2. **Brazing and Soldering**: Induction heating equipment is increasingly used for brazing and soldering operations in electronics manufacturing. The ability to control heating minimizes the risk of damaging heat-sensitive components while achieving strong, reliable joints.
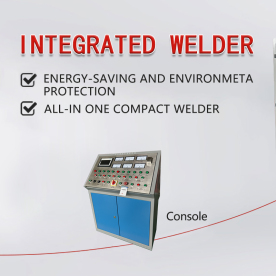
Exploring the Advantages and Applications of Industrial-Grade Induction Heating Equipment in Modern Manufacturing Processes
4. **Joint Heating for Assembly**: In assembly lines, components often require localized heating to fit together smoothly. Induction heating systems can be employed to heat specific areas, facilitating easier assembly without damaging the surrounding material.
5. **Pipe Heating**: Induction heating is also used for heating pipes in preparation for welding or processing. The system heats only the area around the joint, which accelerates the welding process while maintaining the structural integrity of the surrounding material.
Considerations for Implementation
When considering the integration of industrial-grade induction heating equipment into existing processes, manufacturers must evaluate several factors. These include the specific application requirements, the type of materials being processed, the production volume, and the overall energy efficiency goals of the operation. Additionally, investing in high-quality induction heating systems and proper training for operators can significantly enhance performance and safety.

Exploring the Advantages and Applications of Industrial-Grade Induction Heating Equipment in Modern Manufacturing Processes
Industrial-grade induction heating equipment offers numerous benefits that can enhance manufacturing capabilities across various sectors. With its efficiency, precision, and safety features, induction heating is set to play an increasingly significant role in the future of industrial processes. Manufacturers who adopt this innovative technology will be better positioned to meet the evolving demands of modern production while ensuring high-quality standards and operational reliability.