[Solid state HF welder with temperature control]Unlocking Efficiency and Precision: Exploring the Benefits of Solid State HF Welder with Temperature Control in Modern Manufacturing
News 2024-8-11
****In today’s fast-paced manufacturing landscape, the need for technology that enhances efficiency, improves product quality, and reduces operational costs has become increasingly critical. One such innovation that has captured the attention of industries worldwide is the solid state High Frequency (HF) welder equipped with temperature control technology. This advanced welding solution offers a blend of precision, adaptability, and reliability unmatched by conventional techniques. As industries continue to evolve, understanding the advantages brought by a solid state HF welder with temperature control is essential for maintaining a competitive edge.
What is a Solid State HF Welder?
A solid state HF welder operates by generating high-frequency electrical currents through solid-state electronic devices, such as transistors or thyristors. Unlike traditional vacuum tube welders, solid-state systems are more efficient, compact, and reliable. They can provide a consistent power output and can react quickly to changes in the welding environment, making them ideal for tasks requiring high levels of precision.
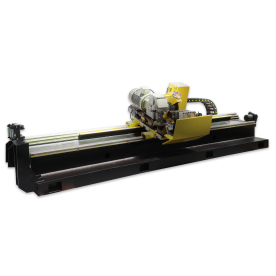
Unlocking Efficiency and Precision: Exploring the Benefits of Solid State HF Welder with Temperature Control in Modern Manufacturing
The Advantages of Temperature Control
1. **Precision in Welding**: The primary advantage of a solid state HF welder with temperature control is precision. The real-time monitoring of temperature ensures that the correct heat is applied to the welding surfaces. This precision is crucial, especially when working with heat-sensitive materials that can warp or degrade if subjected to excessive heat.
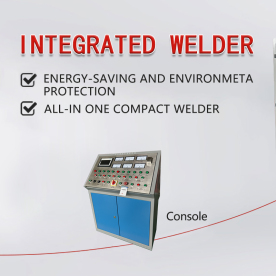
Unlocking Efficiency and Precision: Exploring the Benefits of Solid State HF Welder with Temperature Control in Modern Manufacturing
3. **Improved Quality Control**: Consistent temperature regulation leads to better weld quality. When temperature parameters are controlled accurately, defects such as incomplete seams, bubbling, or excessive melting can be minimized. This quality control is essential for industries where product integrity is paramount, such as automotive, aerospace, and medical device manufacturing.
4. **Energy Efficiency**: Solid state HF welders are typically more energy-efficient than traditional welding machines, primarily due to their rapid response capabilities. The integration of temperature control further maximizes energy efficiency by ensuring that the power is only used when necessary, reducing overall energy consumption and lowering production costs.
5. **Shorter Cycle Times**: Thanks to the rapid heating and cooling capabilities of solid state technology with integrated temperature control, cycle times for welding processes can be significantly shortened. Lesser cycle times translate to increased productivity and the ability to meet high-volume production demands without sacrificing quality.
6. **Minimized Heat-Affected Zones**: In traditional welding processes, the heat-affected zone (HAZ) can be substantial, leading to material degradation. The precise temperature control in solid state HF welders decreases the extent of the HAZ, which is particularly beneficial for maintaining the physical properties of heat-sensitive materials.
7. **User-Friendly Operation**: Modern solid state HF welders with temperature control come equipped with intuitive interfaces that allow operators to set and monitor parameters effortlessly. This ease of use translates to shorter training times for staff and a smoother transition to this advanced technology.
Applications Across Industries
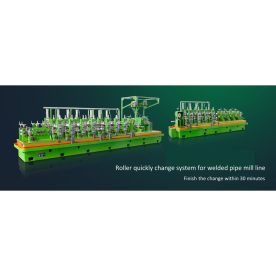
Unlocking Efficiency and Precision: Exploring the Benefits of Solid State HF Welder with Temperature Control in Modern Manufacturing
- **Automotive Manufacturing**: Used for welding plastic components, resulting in light-weight vehicles with improved fuel efficiency. - **Aerospace**: Precision welding of components ensures optimal performance and safety in critical applications. - **Medical Devices**: Sterile environments and strict regulations require high-quality welds, achievable only with precise temperature control. - **Textile Industry**: Joining fabrics and synthetic materials using HF welding bolstered with temperature regulation ensures durability and performance.
Conclusion
The introduction of solid state HF welders with temperature control signifies a significant leap forward in welding technology. With their precision, energy efficiency, and adaptability, these tools are reshaping manufacturing processes across various industries. As the demand for high-quality, consistent, and reliable welds continues to rise, investing in this advanced technology is not just prudent but essential for businesses aiming to thrive in an increasingly competitive environment. Embracing solid state HF welding technology will undoubtedly elevate production capabilities, improve product quality, and harness operational efficiencies that modern manufacturers seek.