[Tube Mill Replacement Parts]A Comprehensive Guide to Tube Mill Replacement Parts: Ensuring Longevity and Efficiency in Your Manufacturing Process
News 2024-8-10
In the expansive world of manufacturing, maintaining the efficiency of machinery is crucial for sustaining production levels and ensuring product quality. Tube mills, specifically, are integral to producing steel pipes and tubes, and their proper functioning is directly linked to the quality of the final product. However, like any industrial equipment, tube mills are subject to wear and tear, necessitating the timely replacement of parts. Understanding tube mill replacement parts is essential for manufacturers seeking to optimize their operations and minimize downtime.
Understanding Tube Mill Functionality
Before diving into the specific replacement parts needed for tube mills, it's important to grasp how these machines operate. Tube mills are designed to take flat strips of metal and convert them into tubular structures. The process involves various rolling and forming operations, where the strips are welded together. Given the mechanical complexity and the stresses involved, these machines require high-quality components that can withstand continuous operation.
Common Tube Mill Replacement Parts
1. **Rolls**: The rolls are one of the most critical components in a tube mill. They shape the flat strip into a tubular form as it moves through various set stations in the mill. Over time, these rolls can develop flat spots or become worn down, which can lead to dimensional inaccuracies in the produced pipe. Regular inspection and timely replacement of rolls can significantly enhance product quality.
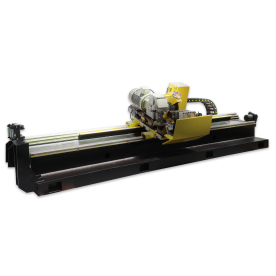
A Comprehensive Guide to Tube Mill Replacement Parts: Ensuring Longevity and Efficiency in Your Manufacturing Process
3. **Bearings**: Bearings facilitate the smooth operation of rolls and other rotating components in tube mills. Continuous usage leads to bearing wear, which can create vibrations and misalignment, negatively affecting production output. Regular checks and replacement of worn bearings can extend the overall lifespan of the tube mill.
4. **Mandrels**: Mandrels are utilized to support the internal structure of the tube while it is being formed. They come under stress during the rolling process, which can lead to bends or breaks. An effective maintenance schedule will involve checking mandrels for wear and damage, ensuring the tubular product's inner dimensions remain accurate.
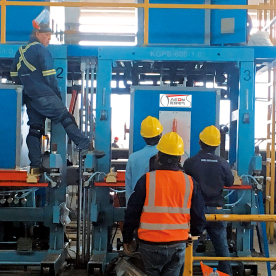
A Comprehensive Guide to Tube Mill Replacement Parts: Ensuring Longevity and Efficiency in Your Manufacturing Process
6. **Roll Change Gear Assemblies**: In tube mills that require periodic roll changes to accommodate different product specifications, the gear assemblies become extremely important. These parts can fail under heavy loads, and having replacements readily available can save valuable production time.
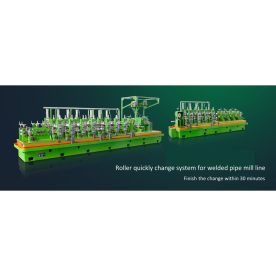
A Comprehensive Guide to Tube Mill Replacement Parts: Ensuring Longevity and Efficiency in Your Manufacturing Process
To ensure the longevity and efficiency of tube mills, manufacturers should adopt best practices for replacement and maintenance. Here are some strategies to consider:
- **Preventive Maintenance**: Regularly scheduled inspections and maintenance can identify wear before it leads to significant failures. Implementing a preventive maintenance program can reduce the frequency of unplanned shutdowns. - **Quality Parts**: When replacing components, always choose high-quality parts from reputable suppliers. Though initially more expensive, quality parts can provide better performance and durability, reducing the need for frequent replacements.
- **Training**: Operators and maintenance personnel should be adequately trained to recognize signs of wear and understand replacement procedures. Knowledgeable staff can carry out necessary maintenance in a timely and effective manner.
- **Inventory Management**: Keeping an inventory of critical spare parts can minimize downtime during replacements. This foresight is especially valuable for businesses that operate continuously or have tight production schedules.
Conclusion
In the competitive landscape of manufacturing, efficient operation of tube mills is essential for maintaining productivity and product quality. Understanding and managing tube mill replacement parts effectively can not only improve longevity but also enhance operational efficiency. By being proactive in maintenance and choosing the right components, manufacturers can mitigate risks and ensure that their tube mills perform at peak efficiency. Regular assessments of wear and tear, coupled with the adoption of best practices for part replacement, will result in a more resilient and productive manufacturing operation.