[Pipe making machine with welding function]Revolutionizing Pipeline Production: The Advantages and Applications of Pipe Making Machines with Welding Function
News 2024-8-10
In today’s fast-paced industrial landscape, the need for efficient and reliable manufacturing processes has never been greater. Among the many innovations in manufacturing technology, pipe making machines with welding functions stand out as a critical advancement. These sophisticated machines play a pivotal role in producing high-quality pipes for various applications, including construction, oil and gas, water supply, and much more. This article delves into the importance, functionality, and benefits of pipe making machines equipped with welding capabilities.
Understanding Pipe Making Machines
Pipe making machines are specialized equipment designed to fabricate pipes from raw materials such as metal, plastic, and other composites. The manufacturing process typically involves forming, welding, and finishing stages to create durable pipes that meet specific industry standards. When enhanced with a welding function, these machines can seamlessly integrate the welding process into the production line, leading to increased efficiency, reduced labor costs, and improved quality control.
Key Components of Pipe Making Machines with Welding Function
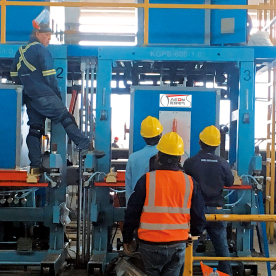
Revolutionizing Pipeline Production: The Advantages and Applications of Pipe Making Machines with Welding Function
2. **Forming Unit**: This section of the machine shapes the raw material into the desired pipe profile. Depending on the design requirements, various processes such as roll forming or extrusion can be used.
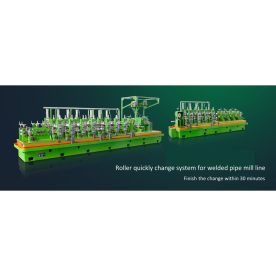
Revolutionizing Pipeline Production: The Advantages and Applications of Pipe Making Machines with Welding Function
4. **Cooling and Finishing**: After welding, pipes must be cooled and finished to ensure they meet specific standards and tolerances. This stage often includes straightening, cutting to length, and quality inspections.
5. **Control System**: Modern pipe making machines come equipped with sophisticated control systems that monitor the entire production process, ensuring consistent quality and allowing for real-time adjustments.
Benefits of Using Pipe Making Machines with Welding Function
1. **Increased Production Efficiency**: The integration of welding functions into pipe making machines allows for a continuous production flow. This reduces downtime associated with manual welding processes and speeds up overall plant operation, enabling manufacturers to meet high-demand requirements swiftly.
2. **Cost-Efficiency**: Combining various functions into a single machine not only simplifies the manufacturing process but also reduces labor costs. Fewer operators are needed to manage the production line as multiple stages are automated.
3. **Superior Quality Control**: Automated welding processes offer higher precision and consistency compared to manual methods. This minimizes defects and ensures that all pipes produced meet stringent quality standards, which is especially important in industries such as oil and gas where leaks can be catastrophic.
4. **Versatility in Manufacturing**: Pipe making machines with welding functions can be adapted to produce different types and sizes of pipes. This flexibility allows manufacturers to respond quickly to changing market demands without the need for considerable reconfiguration or investment in additional machinery.
5. **Enhanced Safety**: Automation in the welding process reduces human involvement in potentially dangerous tasks. This not only enhances the safety of the workplace but also reduces the likelihood of workplace injuries associated with manual welding operations.
Applications of Pipe Making Machines with Welding Function
The versatility of pipe making machines means they can be utilized in various key industries:

Revolutionizing Pipeline Production: The Advantages and Applications of Pipe Making Machines with Welding Function
Conclusion
In conclusion, pipe making machines with welding functions represent a significant technological leap in the manufacturing sector. Their ability to streamline processes, ensure high-quality production, and reduce operational costs makes them indispensable to various industries. As the demand for high-quality pipes continues to grow, the importance of these advanced machines will only increase, solidifying their role in the future of manufacturing. Embracing this technology is essential for manufacturers looking to enhance efficiency and maintain competitiveness in an ever-evolving marketplace.