[Tube mill production line]Understanding the Tube Mill Production Line: Key Components, Benefits, and Applications in Modern Manufacturing
News 2024-8-8
The tube mill production line plays a crucial role in the manufacturing of various types of metal tubes and pipes. As industries demand higher quality products, the need for advanced production technologies has risen significantly. This article delves into the key components, benefits, and applications of the tube mill production line, highlighting its importance in modern manufacturing.
What is a Tube Mill Production Line?
A tube mill production line is a series of machinery and equipment designed to manufacture metal tubes and pipes through a specific process known as tube forming. The process typically involves several stages, including steel strip preparation, tube formation, welding, sizing, and finishing. This production line is widely used for creating various tubular products, including structural pipes, automotive components, and various industrial applications.
Key Components of a Tube Mill Production Line
1. **Steel Strip Preparation**: The process begins with the selection and conditioning of steel strips. Strip preparation involves cleaning, flattening, and sometimes coating the steel before it moves to the forming stage. The quality of the raw material greatly influences the final product's integrity.
2. **Tube Forming**: This stage is where the flat steel strip is shaped into a tube. High-speed forming rollers guide the steel strip around and create a circular shape. The precision of this equipment ensures uniformity and dimensional accuracy in the tubes produced.
3. **Welding**: After the strip has taken shape, the edges are welded together to form a complete tube. Depending on the application, different welding methods can be employed, including high-frequency resistance welding (HFW) or submerged arc welding (SAW). The welding process is crucial as it affects the strength and durability of the final product.
4. **Sizing and Calibration**: Post-welding, the tubes undergo sizing to achieve the desired diameter and wall thickness. This stage often involves using a sizing mill to exert pressure on the tube, ensuring it meets strict tolerances. Accurate sizing is necessary for applications where precision is paramount.
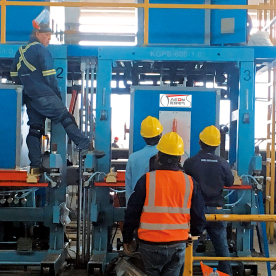
Understanding the Tube Mill Production Line: Key Components, Benefits, and Applications in Modern Manufacturing
Benefits of Tube Mill Production Line
1. **Increased Efficiency**: Tube mill production lines are designed for high-speed operations, which significantly increases the throughput compared to traditional manufacturing methods. This efficiency translates into reduced production costs and shorter lead times.
2. **Versatility**: The tube mill can be adjusted to produce tubes of various sizes, shapes, and thicknesses. This flexibility allows manufacturers to respond quickly to market demands and customize products for specific applications.
3. **High Quality**: Modern tube mills are equipped with advanced technology to inspect and monitor product quality throughout the manufacturing process. This ensures that only the highest quality tubes reach the market, leading to increased customer satisfaction.
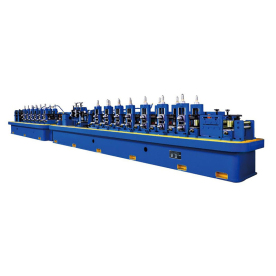
Understanding the Tube Mill Production Line: Key Components, Benefits, and Applications in Modern Manufacturing
Applications of Tube Mill Production Lines
Tube mill production lines are integral in various industries, including:

Understanding the Tube Mill Production Line: Key Components, Benefits, and Applications in Modern Manufacturing
Conclusion
The tube mill production line represents a sophisticated and vital aspect of modern manufacturing, providing a solution for the high demand for metal tubes and pipes across diverse industries. Its key components, such as steel strip preparation, tube forming, welding, sizing, and finishing, work cohesively to produce high-quality products efficiently. As industries continue to evolve, the tube mill production line will undoubtedly remain at the forefront of innovation, ensuring the supply of essential products that support our infrastructure and economy.