[High frequency welder]Exploring the Advantages and Applications of High Frequency Welders in Modern Manufacturing Processes
News 2024-8-7
High frequency welding is a cutting-edge technique that has significantly transformed the landscape of modern manufacturing. The adoption of high frequency welders has led to advancements in various industries, including automotive, aerospace, and textile production. By utilizing high frequency electromagnetic energy, these welders allow for precise and efficient joining of materials that would be challenging to fuse using traditional methods. This article delves into the numerous advantages and applications of high frequency welders, shedding light on why they are increasingly becoming a staple in production facilities worldwide.
What is High Frequency Welding?
High frequency welding, often referred to as RF (radio frequency) welding or dielectric welding, operates by employing high frequency electromagnetic fields to generate heat within a material. This technology is predominantly used for thermoplastic materials, where the molecules are agitated by the electromagnetic energy, causing them to soften and flow together. The process can create strong, durable seams without the need for additional adhesives or fasteners, making it an ideal choice for various manufacturing needs.
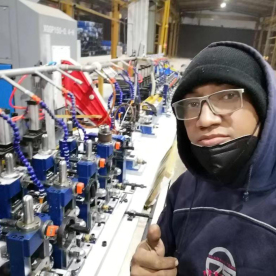
Exploring the Advantages and Applications of High Frequency Welders in Modern Manufacturing Processes
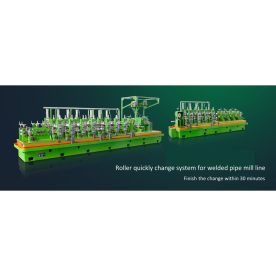
Exploring the Advantages and Applications of High Frequency Welders in Modern Manufacturing Processes
1. **Speed and Efficiency**: One of the most notable benefits of high frequency welders is their speed. The welding process can be executed in a fraction of the time compared to traditional methods. This rapid cycle time boosts overall productivity and allows manufacturers to meet tight deadlines, particularly in high-volume production environments.
2. **Precision and Control**: High frequency welding provides excellent precision, which is essential for creating high-quality seams. The ability to control various parameters such as temperature, pressure, and dwell time ensures that the weld is uniform and consistent. This level of control minimizes the risk of defects, reducing waste and lowering production costs.
3. **Versatility**: High frequency welders can work with a wide range of materials, including PVC, polyurethane, and various other thermoplastics. This versatility makes them suitable for diverse applications, from manufacturing inflatable products to creating medical devices. Manufacturers can adapt the technology to serve different production needs without needing multiple specialized machines.
4. **Cost-Effectiveness**: The elimination of adhesives and fasteners not only reduces material costs but also decreases labor expenses associated with assembly. Furthermore, the increased efficiency means that manufacturers can achieve higher throughput, ultimately resulting in lower per-unit costs.
5. **Strong and Durable Bonds**: The strength of the welds produced by high frequency welders is remarkable. The heat generated during the process forms a strong molecular bond between the materials, resulting in seams that can withstand significant stress and pressure. This strength is particularly advantageous in applications where safety and reliability are paramount.
Applications of High Frequency Welders
High frequency welders find applications in various sectors due to their versatility and efficiency. Some common applications include:
- **Automotive Industry**: In the automotive sector, high frequency welders are utilized to produce components such as airbag covers, seat covers, and other interior parts. The process allows for the creation of complex shapes and designs essential for modern vehicle aesthetics and functionality.
- **Medical Device Manufacturing**: Medical devices require stringent hygiene standards and precise engineering. High frequency welding is employed to produce medical bags, tubing, and components, ensuring that products are free from contaminants and have the necessary strength for their intended use.

Exploring the Advantages and Applications of High Frequency Welders in Modern Manufacturing Processes
- **Packaging**: In packaging, high frequency welding is employed to create seals in food and pharmaceutical packaging. The ability to produce airtight seals ensures product safety and extends shelf life, a critical factor in the consumer goods market.
- **Consumer Goods**: From inflatable toys to soft-sided luggage, many consumer goods that require durable seams leverage high frequency welding technology. This application is pivotal in ensuring that these products can endure everyday use while maintaining their integrity.
Conclusion
In conclusion, high frequency welders represent a revolutionary advancement in manufacturing technology, providing numerous advantages including speed, precision, and versatility. Their widespread applications across diverse industries underscore their significance in modern production. As technology continues to evolve, it is likely that high frequency welding will play an even more pivotal role in shaping innovative manufacturing processes and products. With the increasing demand for efficiency and quality, embracing high frequency welding is not just a trend—it's an essential step toward future-proofing manufacturing operations.