[Roller for tube mill]Understanding the Importance of Roller for Tube Mill: Enhancing Efficiency and Quality in Tube Production Processes
News 2024-8-5
In the world of industrial manufacturing, tube mills play a crucial role in producing a diverse range of tubes and pipes used in various applications, from construction to automotive engineering. One of the most vital components in the operation of a tube mill is the roller. These rollers are key in shaping, forming, and welding the metal strips into finished tubes. Understanding the importance of rollers in tube mills not only highlights their critical role but also sheds light on how they can enhance the efficiency and quality of tube production processes.
The operation of a tube mill involves several stages, including uncoiling, forming, welding, and finishing. Throughout these stages, rollers are essential in providing the necessary force and guidance to the material. The performance of tube mills largely depends on the quality and design of these rollers. Initially designed to handle the raw material—typically flat metal strips—rollers must possess the right shapes and surface finishes to ensure that they can deform the metal without causing damage or defects.
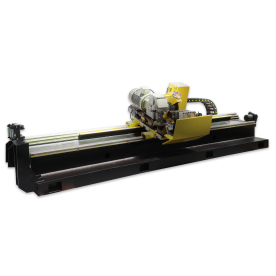
Understanding the Importance of Roller for Tube Mill: Enhancing Efficiency and Quality in Tube Production Processes
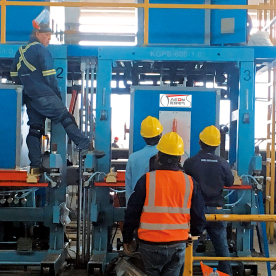
Understanding the Importance of Roller for Tube Mill: Enhancing Efficiency and Quality in Tube Production Processes
A significant aspect of roller design is the alignment of multiple rollers throughout the tube mill. Proper alignment is essential to ensure uniform pressure distribution and consistent shaping of the material. Misalignment can lead to defects, such as uneven wall thickness or even bending of the tube, which is detrimental to the final product's durability and performance. Therefore, maintenance and regular alignment checks of the rollers are crucial for operational efficiency and product quality.
In addition to these mechanical aspects, the role of rollers extends into the welding process that is critical in tube mills. Modern tube mills often utilize high-frequency resistance welding (HFW) methods, where the edges of the formed tube are heated by electrical resistance and then fused together. Here, rollers again are indispensable as they assist in bringing the two edges together, maintaining the appropriate pressure during the welding process to ensure a strong bond. The integrity of the weld joint directly influences the quality of the final product, making the performance of the rollers in this stage particularly vital.
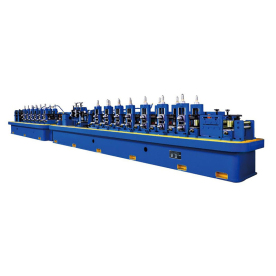
Understanding the Importance of Roller for Tube Mill: Enhancing Efficiency and Quality in Tube Production Processes
In conclusion, rollers are indispensable elements of tube mills that remarkably influence the efficiency and quality of tube production processes. From shaping the raw material to ensuring precise welding operations, the functionality of these rollers resides at the heart of the manufacturing process. As technology advances and the demand for high-quality tubes grows, the importance of optimizing roller design, material, and maintenance will continue to be pivotal in the evolution of tube mills. Manufacturers who emphasize the role of rollers in their production processes are likely to achieve higher efficiency rates, improved product quality, and a competitive edge in the market.