[All-in-one high frequency welder]Exploring the Advantages of the All-in-One High Frequency Welder: Revolutionizing Metal Joining Techniques for Industries
News 2024-8-5
****In the ever-evolving landscape of manufacturing and fabrication, the demand for innovative and efficient welding solutions is increasing. Among the various technologies available, the all-in-one high frequency welder stands out as a versatile tool that enhances productivity, quality, and safety in metal joining processes. This article delves into the many benefits of high frequency welding, its applications across different industries, and the revolutionary role it plays in modern fabrication.
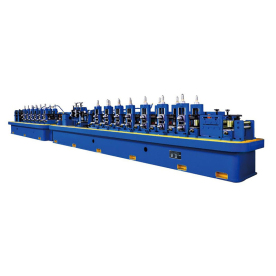
Exploring the Advantages of the All-in-One High Frequency Welder: Revolutionizing Metal Joining Techniques for Industries
High frequency welding, often referred to as RF welding or dielectric welding, is a technique that employs high-frequency electromagnetic waves to heat and fuse materials. This process is primarily used with thermoplastic materials but is also applicable to metals when combined with appropriate techniques. The all-in-one high frequency welder combines several processes and features into one unit, providing users with flexibility and efficiency.
Key Advantages of an All-in-One High Frequency Welder
1. **Versatility**: One of the most significant advantages of an all-in-one high frequency welder is its versatility. It can handle various materials, including plastics, composites, and metals. This adaptability makes it an ideal solution for industries that require different welding processes for various applications.
2. **Increased Efficiency**: Traditional welding methods can be time-consuming. However, an all-in-one high frequency welder accelerates the welding process significantly. The high-frequency currents generate heat quickly, reducing the time required for welding and allowing for faster production cycles. This efficiency leads to reduced labor costs and increased throughput.
3. **Improved Quality of Welds**: High frequency welding produces strong, consistent, and high-quality welds. The precision of the process reduces the possibility of defects and weak points in the joints, ensuring that the finished product meets required standards. This quality is essential in industries that prioritize safety and durability, such as automotive and aerospace.
4. **Space Saving Design**: The all-in-one aspect of this welder means that it consolidates multiple functions into one machine. This design saves valuable floor space in manufacturing environments, allowing companies to declutter and organize their workspace more effectively.
5. **User-Friendly Operation**: Many all-in-one high frequency welders come equipped with advanced controls and intuitive interfaces, making them easier to operate. Operators can quickly learn how to use the machine without extensive training. Many models also feature programmable settings, enabling the replication of specific welding processes with high precision.
Applications Across Industries
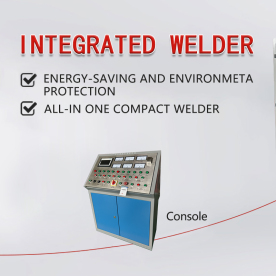
Exploring the Advantages of the All-in-One High Frequency Welder: Revolutionizing Metal Joining Techniques for Industries
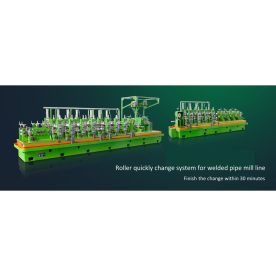
Exploring the Advantages of the All-in-One High Frequency Welder: Revolutionizing Metal Joining Techniques for Industries
- **Automotive Manufacturing**: In the automotive sector, high frequency welders are employed to fabricate components such as airbags, seats, and upholstery. The ability to create strong and reliable joints is crucial for ensuring passenger safety.
- **Aerospace**: The aerospace industry demands the highest quality of materials and welds. High frequency welding is utilized for manufacturing critical components, providing durability and resistance to harsh conditions.
- **Construction**: In construction, particularly for plumbing and electrical applications, the speed and efficiency of high frequency welding can facilitate faster assembly processes, leading to timely project completions.
Conclusion
The all-in-one high frequency welder has undeniably transformed the welding landscape, offering unparalleled advantages in efficiency, quality, and versatility. Its ability to adapt to various materials and processes makes it a vital tool for industries striving for innovation and excellence in fabrication. As the demand for high-quality welded products continues to rise, embracing technologies like the all-in-one high frequency welder will be pivotal in maintaining competitive advantage and driving growth in the global marketplace. Ultimately, investing in such advanced welding solutions paves the way for more robust, reliable, and efficient manufacturing processes, aligning businesses with the future of industrial fabrication.