[Industrial tube making machinery]Understanding the Innovations and Applications of Industrial Tube Making Machinery in Modern Manufacturing Processes
News 2024-8-5
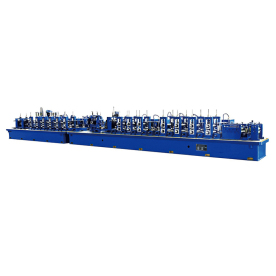
Understanding the Innovations and Applications of Industrial Tube Making Machinery in Modern Manufacturing Processes
Industrial tube making machinery plays a pivotal role in the manufacturing sector, facilitating the production of various tube and pipe materials that are fundamental to numerous applications across multiple industries. From automotive and aerospace to construction and plumbing, these machines have evolved significantly over the years, incorporating advanced technologies that enhance efficiency, precision, and versatility. This article delves into the innovations, processes, and applications of industrial tube making machinery, highlighting its significance in contemporary manufacturing.
At the heart of tube making machinery lies the challenge of transforming raw materials into functional, high-quality products. Tubes are essential components used for conveying fluids and gases, structural applications, and even decorative purposes. The primary materials used in tube production include metals, plastics, and composites, each requiring distinct manufacturing processes and machinery.
One of the primary innovations in the realm of industrial tube making machinery is the adoption of computer numerical control (CNC) systems. CNC technology enables machines to operate with a high degree of automation and precision, allowing manufacturers to produce tubes with intricate designs and specifications. This advancement has significantly reduced lead times and minimized errors, which are crucial in industries where precision is paramount, such as aerospace and medical device manufacturing.
In addition to CNC technology, the development of laser cutting and welding systems has revolutionized the tube making process. Laser technology allows for exceptionally fine cuts, enabling manufacturers to create complex profiles without compromising the material’s integrity. This process is particularly advantageous in industries where tight tolerances are required. Furthermore, laser welding techniques have replaced traditional welding methods in many applications, offering cleaner, stronger joints that enhance the overall quality and durability of the finished product.
Another notable trend in industrial tube making machinery is the growing emphasis on sustainability and energy efficiency. Manufacturers are increasingly adopting eco-friendly practices, reflecting a broader shift toward sustainable manufacturing. Advanced tube making machines are designed to minimize waste, utilize energy efficiently, and recycle materials whenever possible. Many machines now incorporate features such as closed-loop systems, which recapture and reuse waste materials, significantly reducing the environmental impact of production.
The versatility of industrial tube making machinery allows for the fabrication of an extensive range of products. From simple cylindrical tubes to more complex shapes such as square and rectangular tubes or even custom profiles, the machinery can adapt to varied requirements. This flexibility is particularly important as industries demand more specialized solutions tailored to their specific needs. For example, the automotive sector frequently requires unique tube shapes for shock absorbers and exhaust systems, necessitating machinery that can accommodate these specifications.
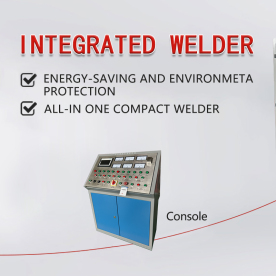
Understanding the Innovations and Applications of Industrial Tube Making Machinery in Modern Manufacturing Processes
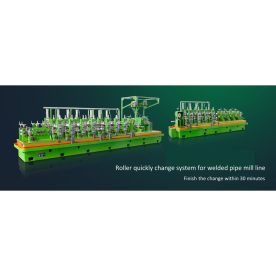
Understanding the Innovations and Applications of Industrial Tube Making Machinery in Modern Manufacturing Processes
In summary, industrial tube making machinery is an essential component of modern manufacturing that supports a plethora of industries. Innovations such as CNC technology, laser cutting and welding, and an emphasis on sustainability are transforming the way tubes are produced. With versatility that allows for the production of a wide range of products, and a commitment to precision and quality, these machines not only meet current demands but also pave the way for future advancements in manufacturing processes. As industries continue to evolve, the importance of investing in advanced tube making machinery will only increase, ensuring that manufacturers can meet the challenges of tomorrow with confidence and efficiency.