[Stainless steel pipe mill production line]Understanding the Stainless Steel Pipe Mill Production Line: Processes, Equipment, and Benefits
News 2024-8-4
Introduction
In the realm of industrial manufacturing, the importance of stainless steel pipe production cannot be overstated. A stainless steel pipe mill production line is integral to producing pipes that meet a wide variety of applications, from construction to oil and gas. This article delves into the intricacies of a stainless steel pipe mill production line, exploring the various processes involved, the equipment utilized, and the advantages it brings to manufacturers and end-users alike.
Overview of the Stainless Steel Pipe Mill Production Line
A stainless steel pipe mill production line is a sophisticated array of machines and technologies dedicated to manufacturing stainless steel pipes of various sizes and specifications. The production line typically consists of several stages, including raw material preparation, pipe forming, welding, and finishing processes. Each stage plays a crucial role in ensuring that the final product meets the quality requirements of various industrial applications.
Raw Material Preparation
The primary raw material for manufacturing stainless steel pipes is stainless steel billets, coils, or sheets. These raw materials often undergo multiple tests to ensure their chemical composition and mechanical properties are suitable for the intended use. Once the raw materials are approved, they are processed into a form that is ready for pipe production. This process may include cutting the coils or sheets into manageable sizes and removing any surface imperfections, ensuring a uniform starting point for the subsequent manufacturing stages.
Pipe Forming
The pipe forming stage is where the real action begins in a stainless steel pipe mill production line. The prepared raw materials are fed into advanced forming machines that manipulate them into the desired pipe shape. Several forming techniques may be employed, including:
1. **Seamless Pipe Formation**: In this method, a solid round billet is heated and pierced, creating a hollow tube. The tube is then elongated and shaped into a seamless pipe, which is often preferred for high-pressure applications due to its strength and durability.
2. **Welded Pipe Formation**: This technique involves flattening the rolled steel sheets and then forming them into a tubular shape. The edges are then welded together using various methods such as TIG, MIG, or resistance welding. Welded pipes are widely used in various sectors due to their cost-effectiveness and flexibility in production.
Welding Process
In the case of welded pipes, the welding process is a critical component. It ensures that the pipes achieve the desired strength and can withstand various pressures and corrosive environments. Depending on the specifications required, manufacturers may employ different welding technologies to ensure the integrity and reliability of the joints. Furthermore, the welding process also involves inspection and testing procedures, such as non-destructive testing, to confirm that there are no flaws in the welds.
Finishing Processes
Once the pipes are formed and welded, they undergo various finishing processes that enhance their appearance and performance. Common finish treatments include:
1. **Pickling and Passivation**: This chemical treatment removes surface scale and impurities, providing a clean, polished surface that enhances corrosion resistance.
2. **Annealing**: A heat treatment process that alleviates residual stresses and enhances the pipe's mechanical properties. Annealing allows for better formability and durability in the end product.
3. **Cutting and Beveling**: Pipes are often cut to specific lengths and may require beveled edges for easy installation in various applications.
Quality Control
Quality control is a vital aspect of the stainless steel pipe mill production line. Rigorous testing is conducted at various stages of production, with checks on dimensions, surface quality, and mechanical properties. This ensures that the products meet international standards and customer specifications.
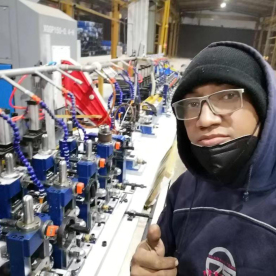
Understanding the Stainless Steel Pipe Mill Production Line: Processes, Equipment, and Benefits
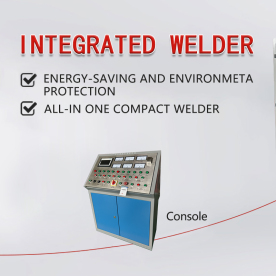
Understanding the Stainless Steel Pipe Mill Production Line: Processes, Equipment, and Benefits
1. **Versatility**: Manufacturers can produce a wide range of pipe sizes and specifications to meet diverse industry needs.
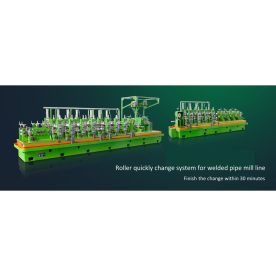
Understanding the Stainless Steel Pipe Mill Production Line: Processes, Equipment, and Benefits
3. **Durability and Corrosion Resistance**: Stainless steel pipes exhibit exceptional strength, making them suitable for high-pressure applications while resisting corrosion, ensuring longevity.
4. **Improved Efficiency**: Modern pipe mill production lines are often automated, increasing output and streamlining operations.
Conclusion
The stainless steel pipe mill production line represents a critical component of modern manufacturing, enabling the production of high-quality, durable pipes necessary for a variety of applications. Understanding the processes involved in this production line highlights not only the technology that drives efficiency but also the commitment to quality that manufacturers must uphold. As industries continue to evolve, the role of stainless steel will undoubtedly remain central, and the production lines that create these essential components will only become more sophisticated.