[Customized induction heating equipment]Exploring the Advancements and Benefits of Customized Induction Heating Equipment in Modern Manufacturing Processes
News 2024-8-4
****Induction heating has become an integral part of various manufacturing processes, particularly in metalworking, automotive, and electronics industries. The technology offers significant advantages, including efficiency, precision, and reduced energy consumption. As industries continue to evolve, the demand for tailored solutions has led to a surge in the development of customized induction heating equipment. This article delves into the advancements in induction heating technology, the benefits it offers, and the importance of customization to meet specific industrial needs.
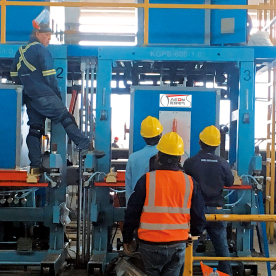
Exploring the Advancements and Benefits of Customized Induction Heating Equipment in Modern Manufacturing Processes
One of the key advantages of customized induction heating equipment is the ability to adapt the technology to unique production processes. Manufacturers often face specific challenges that standardized equipment may not adequately address. For example, the size, shape, and material composition of parts can vary widely, requiring induction heating solutions that are designed to cater specifically to these variations. Customization allows for the creation of coils and heating systems that account for factors such as geometry, heating speed, and temperature uniformity.
Furthermore, customized induction heating equipment can enhance process efficiency. By designing systems that are tailored to a specific application, manufacturers can reduce heating times, minimize energy consumption, and improve the overall quality of the final product. For instance, in the automotive industry, induction heating is often used for the hardening of crankshafts and axles. Customized systems can optimize the heating profile, ensuring that the parts achieve the desired hardness without any thermal distortion or damage.
Another significant benefit of customized induction heating solutions is the ability to integrate advanced control technologies. Modern induction heating systems are increasingly equipped with sophisticated software and sensors that enable precise temperature control and monitoring. Custom solutions can incorporate these technologies to offer real-time feedback, ensuring that operators can maintain optimal heating conditions throughout the process. This level of control not only enhances product quality but also contributes to better process management and sustainability.
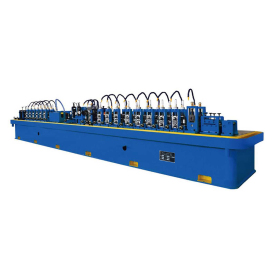
Exploring the Advancements and Benefits of Customized Induction Heating Equipment in Modern Manufacturing Processes
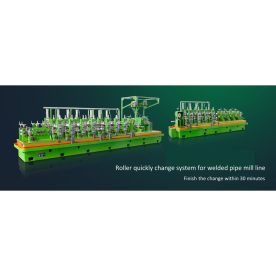
Exploring the Advancements and Benefits of Customized Induction Heating Equipment in Modern Manufacturing Processes
In addition to these operational advantages, customized induction heating equipment also offers economic benefits. While the initial investment can be higher than traditional methods, the long-term savings can be substantial. Enhanced efficiency, reduced energy consumption, and improved product quality often translate into lower production costs. Additionally, shorter processing times can lead to increased throughput, enabling manufacturers to meet growing market demands more effectively.
As the technology surrounding customized induction heating equipment continues to advance, the opportunities for manufacturers are expanding. Emerging technologies such as smart manufacturing, artificial intelligence, and the Internet of Things (IoT) are beginning to integrate with induction heating systems, creating even more customized solutions that are capable of self-diagnosis, predictive maintenance, and seamless operation within larger automated processes.
In conclusion, customized induction heating equipment is reshaping the landscape of modern manufacturing. As industries seek to optimize production processes, improve product quality, and prioritize sustainability, the ability to tailor induction heating solutions to specific applications has never been more crucial. The advancements in this technology promise not only to enhance efficiency and reduce costs but also to pave the way for a more innovative and sustainable manufacturing future. Investing in customized solutions allows companies to stay competitive in a rapidly evolving market while meeting the ever-increasing expectations of quality and performance.