[Industrial All-in-one High Frequency Welder]Exploring the Revolutionary Advancements of Industrial All-in-one High Frequency Welder for Enhanced Manufacturing Efficiency
News 2024-8-3
Introduction
In the ever-evolving landscape of manufacturing and industrial processes, efficiency and precision are paramount. Enter the Industrial All-in-one High Frequency Welder, a game-changing tool designed to meet the demanding needs of modern industries. This comprehensive article delves into the features, advantages, and applications of this innovative equipment, highlighting how it enhances productivity, reduces costs, and improves the quality of welds.
What is an Industrial All-in-one High Frequency Welder?
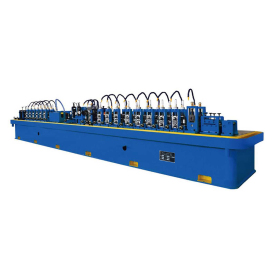
Exploring the Revolutionary Advancements of Industrial All-in-one High Frequency Welder for Enhanced Manufacturing Efficiency
Key Features of Industrial All-in-one High Frequency Welder
1. **Versatility in Welding Types**: One of the most significant advantages of an Industrial All-in-one High Frequency Welder is its ability to handle multiple welding types, including but not limited to, high-frequency induction welding, capacitance welding, and high-speed spot welding. This versatility makes it suitable for a wide range of materials, such as metals, plastics, and composites.
2. **Advanced Control Systems**: These welders come equipped with state-of-the-art control systems that allow for precise adjustments to voltage, frequency, and welding speed. This ensures that operators can customize the welding parameters according to the specifications of each job, resulting in fewer defects and higher-quality outcomes.
3. **Compact Design**: The all-in-one design signifies a remarkable reduction in space without compromising functionality. This feature is particularly beneficial for manufacturing plants where space is at a premium. The reduced footprint also allows for easy transportation and relocation within the facility.
4. **Energy Efficiency**: Industrial All-in-one High Frequency Welders are designed to be energy-efficient, utilizing advanced technology to minimize electricity consumption. This not only helps in reducing operational costs but also aligns with global efforts to promote sustainable manufacturing practices.
5. **User-Friendly Interface**: The incorporation of user-friendly interfaces and touchscreen controls means that operators of various skill levels can quickly learn to use the equipment efficiently. This is essential for maximizing productivity and minimizing downtime during training periods.
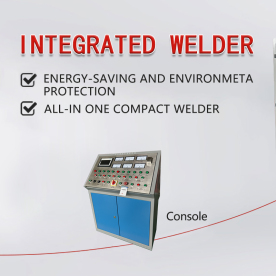
Exploring the Revolutionary Advancements of Industrial All-in-one High Frequency Welder for Enhanced Manufacturing Efficiency
1. **Increased Productivity**: By allowing for multiple welding types with a single machine, companies can streamline their workflow, reducing the time spent on switching between different welding methods and machines.
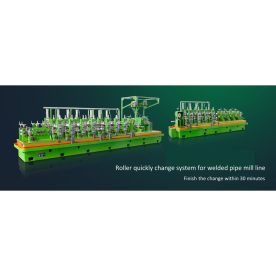
Exploring the Revolutionary Advancements of Industrial All-in-one High Frequency Welder for Enhanced Manufacturing Efficiency
3. **Enhanced Quality**: The precision and control offered by these welders translate into higher quality welds, adhering to stringent industry standards. This is particularly crucial in sectors such as automotive and aerospace, where safety and reliability are non-negotiable.
4. **Adaptability**: As manufacturing demands evolve, the adaptability of an Industrial All-in-one High Frequency Welder allows companies to pivot to new projects or materials without extensive re-investment in additional equipment.
Applications Across Industries
The versatility of Industrial All-in-one High Frequency Welders means they are applicable in various sectors. In construction, these welders are commonly used for joining metal frameworks and structures. The automotive industry utilizes them for welding components due to the need for high-frequency applications that enhance durability and performance.
In electronics, high-frequency welding is critical for producing lightweight yet strong connections in devices. Further, the textile industry is increasingly using these welders to join synthetic fabric, making them essential for manufacturers producing high-quality garments.
Conclusion
The Industrial All-in-one High Frequency Welder represents a significant milestone in advancements in manufacturing technology. With its multifaceted capabilities, energy efficiency, and superior weld quality, it not only meets the diverse needs of modern industries but also sets the stage for future innovations in welding technology. As industries continue to push for enhanced productivity and quality, investing in such high-tech equipment is becoming increasingly vital for staying competitive in the market.