[High-Wear-Resistant Spare Parts for Tube Mills]High-Wear-Resistant Spare Parts for Tube Mills: Enhancing Longevity and Efficiency in Manufacturing Processes
News 2024-8-1
****In the world of manufacturing, particularly in industries reliant on tube mills, the materials and components utilized can significantly affect productivity, quality, and overall operational efficiency. One of the critical requirements for maintaining high performance in these facilities is the use of high-wear-resistant spare parts for tube mills. As industries continue to evolve and demand more from their machinery, investing in superior-quality spare parts becomes imperative.
Understanding Tube Mills and Their Challenges
Tube mills are widely employed to create metal tubes and pipes used in various applications, from construction to automotive manufacturing. These mills operate under extreme conditions, dealing with significant wear and tear due to high-speed processes, large volumes of materials, and abrasive environments. Consequently, the components of tube mills often require frequent maintenance and replacement. Regular wear can lead to diminished performance, increased downtime, and ultimately, higher operational costs.
The harsh working conditions of tube mills necessitate the use of spare parts that can withstand substantial wear and resist premature failure. This is where high-wear-resistant spare parts come into play, designed to optimize the longevity and reliability of tube mills.
Importance of High-Wear-Resistant Spare Parts
The choice of spare parts can directly impact the operational efficiency of tube mills. High-wear-resistant spare parts are crafted from advanced materials that offer superior hardness and resilience, significantly extending their effective lifespan. Here are several key benefits of utilizing such components:
1. **Increased Durability:** The use of high-performance materials allows these parts to resist wear from abrasive materials, thereby maintaining their integrity for longer periods.
2. **Reduced Downtime:** With longer-lasting spare parts, manufacturers can expect fewer breakdowns and maintenance interruptions, allowing production to continue without interruptions.
3. **Enhanced Product Quality:** High-wear-resistant components help maintain consistent operational parameters, ensuring that the tubes produced meet the required specifications without defects.
4. **Cost Efficiency:** Although the initial investment may be higher, the long-term savings resulting from reduced maintenance costs and lower frequency of replacements make high-wear-resistant spare parts a more economical choice over time.
5. **Improved Safety:** Reliable components reduce the risk of component failures that could lead to accidents or equipment damage, contributing to a safer working environment.
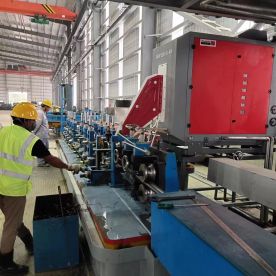
High-Wear-Resistant Spare Parts for Tube Mills: Enhancing Longevity and Efficiency in Manufacturing Processes
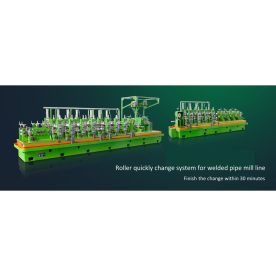
High-Wear-Resistant Spare Parts for Tube Mills: Enhancing Longevity and Efficiency in Manufacturing Processes
- **Roller Bearings:** These are crucial for reducing friction between moving parts and are commonly exposed to heavy loads and wear. High-performance polymer or ceramic bearings can provide improved longevity.

High-Wear-Resistant Spare Parts for Tube Mills: Enhancing Longevity and Efficiency in Manufacturing Processes
- **Cutting Tools:** The components that cut or shape the tubes must maintain sharpness and resist chipping or dullness. Carbide-tipped tools with special coatings can significantly extend their service life.
- **Chutes and Hoppers:** These components often come into contact with abrasive raw materials. Systems constructed from high-strength alloys or lined with wear-resistant materials can prevent rapid degradation.
- **Welded joints and fixtures:** Using advanced welding techniques and wear-resistant materials can ensure that these components last longer under high-pressure conditions.
Innovations in Wear-Resistant Materials
The materials science industry continually works to develop new alloys and coatings that provide enhanced wear resistance. Innovations such as nanotechnology have led to the creation of composites that exhibit outstanding hardness and flexibility, making them suited for demanding applications in tube mills. Additionally, advanced surface treatments can significantly boost the durability of traditional materials, providing a dual benefit of cost-effectiveness and enhanced performance.
Conclusion
In conclusion, the importance of high-wear-resistant spare parts for tube mills cannot be overstated. The longevity and efficiency these components provide play a pivotal role in maintaining a manufacturing facility’s productivity and reducing operational costs. For businesses looking to enhance their tube mill operations, investing in these superior-quality spare parts is not only a practical choice but a strategic one that can yield substantial returns over time. By focusing on durability, performance, and safety, manufacturers can ensure they remain competitive in today's fast-paced industrial landscape.