[High-capacity Pipe mill production line]Exploring the Innovations and Advantages of High-Capacity Pipe Mill Production Lines in Modern Manufacturing
News 2024-8-1
****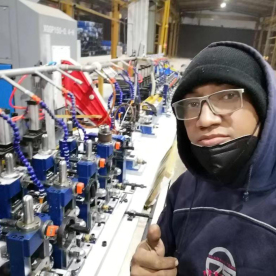
Exploring the Innovations and Advantages of High-Capacity Pipe Mill Production Lines in Modern Manufacturing
High-capacity pipe mill production lines are specialized manufacturing systems designed to produce pipes at an accelerated pace without sacrificing quality. These production lines incorporate advanced technologies, including automation, robotics, and precision engineering, enabling manufacturers to produce large volumes of pipes while maintaining consistency in quality and performance. The production line typically consists of several interconnected stages, including billet feeding, heating, forming, welding, sizing, and quality inspection.
One of the most noteworthy innovations in high-capacity pipe mill production lines is the implementation of automated systems that control various aspects of the manufacturing process. Automation reduces the risk of human error and enhances operational efficiency by allowing for real-time monitoring and adjustments. For instance, automated material handling systems ensure that raw materials are efficiently transported through the production stages, while sensors and control systems manage temperature and speed parameters, ensuring optimal processing conditions.
Another key advancement in these production lines is the utilization of modern forming and welding techniques. Traditional methods, such as manual welding, have been largely replaced by high-frequency induction welding and submerged arc welding technologies. These methods not only improve the overall welding quality but also significantly increase production speeds. The high-frequency induction welding process, for example, allows for rapid heating and bonding of the pipe edges, resulting in a seamless and robust weld, which is particularly crucial in applications involving high-pressure and high-temperature conditions.
The efficiency of high-capacity pipe mill production lines is further enhanced by their ability to produce a diverse range of pipe sizes and materials. Manufacturers can customize their production lines to handle various diameters, wall thicknesses, and materials, such as carbon steel, stainless steel, and even specialized alloys. This versatility allows businesses to cater to different industries and requirements, adapting quickly to market shifts and customer demands.
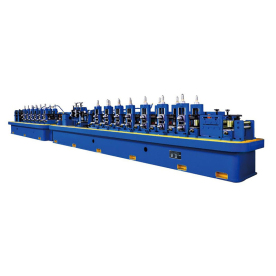
Exploring the Innovations and Advantages of High-Capacity Pipe Mill Production Lines in Modern Manufacturing
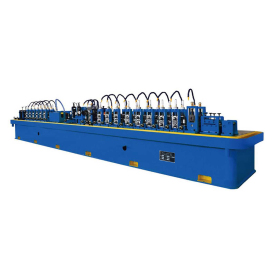
Exploring the Innovations and Advantages of High-Capacity Pipe Mill Production Lines in Modern Manufacturing
Furthermore, the integration of advanced quality control measures within the production line cannot be overlooked. Automated inspection systems have become increasingly sophisticated, utilizing technologies such as ultrasonic testing, radiographic analysis, and computer vision. These systems ensure that each pipe produced meets stringent industry standards, thereby minimizing the risk of defects and maintaining customer satisfaction. Proactive quality assessment also helps manufacturers avoid costly recalls and damages associated with substandard products.
In conclusion, high-capacity pipe mill production lines represent a transformative development in the manufacturing sector. Their innovative technologies, enhanced efficiencies, and cost-effectiveness make them indispensable for meeting the growing demand for high-quality pipes across various industries. As manufacturers continue to invest in these advanced systems, we can expect to see even more innovations that further optimize operational processes, improve product quality, and ultimately, drive global industrial growth. The future of pipe manufacturing indeed appears bright, propelled by the ongoing evolution of high-capacity pipe mill production lines.