[Advanced induction heating equipment technology]Exploring Advanced Induction Heating Equipment Technology: Revolutionizing Industrial Processes and Enhancing Efficiency in Manufacturing
News 2024-8-1
****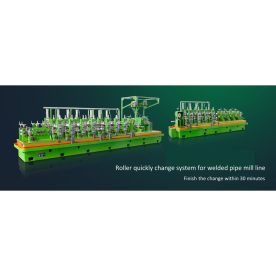
Exploring Advanced Induction Heating Equipment Technology: Revolutionizing Industrial Processes and Enhancing Efficiency in Manufacturing
Induction heating operates on the basic premise of electromagnetic induction, where alternating magnetic fields create eddy currents in conductive materials, causing them to heat up without the need for direct contact with a heating element. This fundamental aspect of the technology leads to significant improvements in efficiency, productivity, and safety in various industries, including automotive, aerospace, metalworking, and food processing.
One of the most notable benefits of advanced induction heating equipment is its energy efficiency. Traditional heating methods often waste a substantial amount of energy through convection and conduction. In contrast, induction heating transfers energy directly to the workpiece, significantly reducing heat loss. Research indicates that induction heating systems can achieve efficiencies of up to 90%, allowing manufacturers to lower their energy consumption and reduce overall operational costs. This increased efficiency is especially crucial in today’s economy, where lowering energy costs can significantly impact the bottom line.
Moreover, precision is a hallmark of induction heating technology. Unlike conventional heating methods that can lead to uneven heat distribution, advanced induction heating equipment provides uniform heating throughout the material being processed. This uniformity is crucial for processes such as hardening, melting, and forging, where even slight variations in temperature can lead to defective products. Advanced induction systems can be finely tuned to ensure that specific areas of a workpiece receive the required amount of heat, thus improving product quality and reducing waste.
Advanced induction heating equipment also enhances the speed of manufacturing processes. Conventional heating methods often require substantial time for heat-up and cooldown. However, induction heating systems can achieve desired temperatures in a fraction of the time. This rapid heating not only increases production rates but also reduces cycle times, enabling manufacturers to meet tight deadlines and respond more quickly to market demands.
Safety is another critical advantage of advanced induction heating technologies. The process generates heat within the material itself rather than from an external source, reducing the risk of burns and other heat-related injuries for operators. Additionally, because there are no open flames or high-temperature surfaces, the potential for fire hazards is significantly lower. This intrinsic safety feature aligns well with modern manufacturing protocols that prioritize worker safety and compliance with environmental regulations.
The versatility of advanced induction heating technologies is noteworthy. These systems can be designed and optimized for various applications, including brazing, soldering, heat treating, and even cooking processes. Manufacturers can customize their induction heating equipment to suit specific needs, which is particularly valuable in niche applications where standard heating methods may fall short.
Furthermore, advancements in control technology have propelled the effectiveness of induction heating systems. Modern equipment is equipped with sophisticated software and sensors that enable real-time monitoring and adjustment of temperature and power output. This level of control not only enhances operational efficiency but also provides critical data that can be used for quality assurance and process optimization.

Exploring Advanced Induction Heating Equipment Technology: Revolutionizing Industrial Processes and Enhancing Efficiency in Manufacturing
