[Solid State HF Welder Replacement Parts]Essential Guide to Solid State HF Welder Replacement Parts: Keeping Your Equipment Running Smoothly for Optimal Performance
News 2024-7-31
****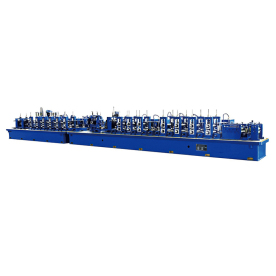
Essential Guide to Solid State HF Welder Replacement Parts: Keeping Your Equipment Running Smoothly for Optimal Performance
Understanding Solid State HF Welders
Solid State HF welders utilize high-frequency electrical currents to join materials, typically metals, through a process known as induction welding. Unlike traditional welding methods that may rely on a combination of heat and pressure, HF welding is characterized by its speed and precision, making it ideal for thin materials that are difficult to join through other means. The simplicity of the process and the compact design of solid-state technology help manufacturers achieve high throughput while minimizing energy consumption.
Importance of Replacement Parts
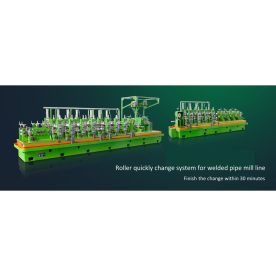
Essential Guide to Solid State HF Welder Replacement Parts: Keeping Your Equipment Running Smoothly for Optimal Performance
Common Solid State HF Welder Parts Needing Replacement
1. **Oscillator**: This is the heart of the welder, responsible for generating high-frequency currents. If the oscillator fails, it can severely interrupt the welding process, making it crucial to have a replacement part on hand.
2. **Capacitors**: Capacitors store and discharge energy needed for welding operations. Over time, capacitors can lose their ability to hold charge, leading to inconsistent performance. Regularly checking and replacing these components can prevent work delays.
3. **Transformers**: Serving to step up or down the voltage required for successful welding, transformers can experience wear from prolonged use or mechanical stresses. Inspecting them periodically and replacing faulty transformers is essential to maintain a stable welding process.
4. **Cooling Systems**: Many Solid State HF welders incorporate cooling systems to prevent overheating. If the cooling fans or water circulation units fail, the welder is at risk of overheating, which could damage sensitive components.
5. **Electrodes**: The electrodes are critical for creating the weld. Depending on the materials being welded, these can wear out or become contaminated. Regular inspection and timely replacement ensure clean and effective welding.
6. **Control Panels**: Any malfunction in the control panel can prevent the welder from functioning correctly. If buttons, displays, or any electronic elements show wear or failure, replacing them promptly can save you time and expenses related to unplanned downtimes.
Maintenance Tips to Extend Equipment Life

Essential Guide to Solid State HF Welder Replacement Parts: Keeping Your Equipment Running Smoothly for Optimal Performance
- **Clean the Equipment**: Dust, debris, and welding slag can accumulate in and around your welder, affecting its performance. Regular cleaning can prevent overheating and ensure optimal operation.
- **Use Quality Parts**: Always opt for OEM replacement parts to ensure that your welder operates to its full potential. Substituting lower-quality parts can lead to performance issues and may void warranties.
- **Monitor Performance**: Keep an eye on your welder’s performance. Unusual noises, inconsistent weld quality, or increased energy consumption may indicate the need for immediate service.
- **Documentation**: Keep a detailed maintenance log with the service history of your welder. Documenting parts replaced and service performed allows you to pinpoint trends and schedule future maintenance effectively.
Conclusion
Having a solid understanding of Solid State HF welder replacement parts is essential for anyone in the manufacturing or welding industry. By proactively maintaining and replacing worn components, you can ensure that your equipment continues to perform at an optimal level, ultimately leading to higher quality welds and increased productivity. Prioritizing quality parts and diligent maintenance practices can keep your Solid State HF welder running smoothly for years to come.