[Integrated pipe mill production line system]Understanding the Integrated Pipe Mill Production Line System: Transforming the Efficiency and Quality of Pipe Manufacturing
News 2024-7-31
In the competitive landscape of manufacturing, the need for efficient production processes is paramount. Among various manufacturing technologies, the Integrated Pipe Mill Production Line System has emerged as a transformative solution, streamlining the production of pipes with enhanced efficiency and quality. This article delves into the components and advantages of the integrated system, its significance in today’s manufacturing environment, and how it marks a shift toward smarter manufacturing.
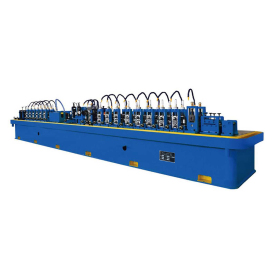
Understanding the Integrated Pipe Mill Production Line System: Transforming the Efficiency and Quality of Pipe Manufacturing
One of the key components of an integrated pipe mill production line is the advanced welding technology. Welding is crucial in pipe manufacturing, as it determines the strength and integrity of the final product. The latest integrated systems utilize advanced welding techniques, such as high-frequency induction welding, which is known for its speed and reliability. This method not only reduces production time significantly but also ensures that the weld quality meets stringent industry standards.
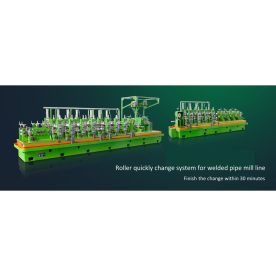
Understanding the Integrated Pipe Mill Production Line System: Transforming the Efficiency and Quality of Pipe Manufacturing

Understanding the Integrated Pipe Mill Production Line System: Transforming the Efficiency and Quality of Pipe Manufacturing
The environmental impact of manufacturing processes is a growing concern. The integrated pipe mill production line addresses sustainability through energy-efficient technologies and waste reduction practices. By streamlining the production process and minimizing handling, manufacturers can significantly reduce energy consumption. Additionally, the recycling of scrap material is maximized within the system, further contributing to environmentally friendly manufacturing practices.
The financial implications of implementing an Integrated Pipe Mill Production Line System are profound. By reducing production times, minimizing waste, and ensuring higher quality outputs, manufacturers can improve profit margins significantly. Furthermore, the system’s ability to adapt to various production scales means that businesses can maintain flexibility in responding to market demands without incurring substantial overhead costs.
In terms of workforce implications, the integration of automation and advanced technology does not entirely replace human workers but enhances their roles. Operators skilled in managing automated systems are in high demand. Moreover, with intelligent production systems that collect and analyze production data, manufacturers can further optimize their operations. The use of Industry 4.0 principles ensures that decision-making is driven by data, thereby enhancing overall operational efficiency.
In conclusion, the Integrated Pipe Mill Production Line System is revolutionizing the pipe manufacturing sector. By combining advanced technologies with traditional processes, manufacturers can achieve unprecedented levels of efficiency, quality, and sustainability. As industries continue to evolve towards smarter, more integrated systems, the integrated pipe mill production line stands out as a model of innovation, adaptability, and productivity in the manufacturing world. As the need for high-quality pipes increases across various sectors, the investment in such integrated systems will likely deliver significant returns in the form of competitiveness and profitability, setting a new standard in pipe manufacturing excellence.