[Tube mill production line]An In-Depth Guide to Tube Mill Production Line: Understanding Its Components, Benefits, and Applications in Modern Manufacturing
News 2024-7-31
****The tube mill production line is a crucial part of the manufacturing process for various industries, including construction, automotive, and pipeline sectors. It is designed for the efficient production of seamless or welded tubes and pipes, which are essential components in numerous applications. This article explores the various aspects of tube mill production lines, including their components, advantages, and applications, illustrating why they are vital in today’s manufacturing landscape.
Understanding Tube Mill Production Lines
A tube mill production line primarily consists of several significant components that work in tandem to process raw materials into finished products. The most fundamental stages of tube production include:
1. **Material Preparation**: This stage involves the selection and preparation of raw materials, typically steel coils or sheets, which are cut to precise lengths before being fed into the tube mill.
2. **Forming**: After preparation, the steel strips are formed into a tube shape using rollers. A set of forming rolls progressively shapes the strip into a circular form while simultaneously ensuring alignment and consistency in dimensions.
3. **Welding**: Once the strip is shaped into a tube, the edges are welded together. There are various welding techniques employed, such as high-frequency induction welding or laser welding, which create a strong bond capable of withstanding high pressure.
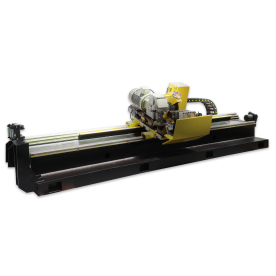
An In-Depth Guide to Tube Mill Production Line: Understanding Its Components, Benefits, and Applications in Modern Manufacturing
5. **Cutting and Finishing**: The final stages involve cutting the welded tubes to specific lengths and applying finishing processes. This may include treatments such as galvanization, painting, or coating to enhance performance and corrosion resistance.
6. **Quality Control**: Rigorous testing is fundamental to ensure that the produced tubes meet industry standards. Quality control measures include dimensional checks, pressure testing, and visual inspections.
Benefits of Tube Mill Production Lines
The adoption of tube mill production lines offers numerous advantages, making them a preferred choice in numerous manufacturing environments:
- **Efficiency and Speed**: Modern tube mills are automated and can produce tubes at a remarkable speed, often measuring output in kilometers per hour. This efficiency allows manufacturers to meet large-scale demands promptly.
- **Cost-effectiveness**: By streamlining the production process, tube mills reduce labor and manufacturing costs. The use of high-quality raw materials minimizes waste and maximizes yield, contributing to overall profitability.
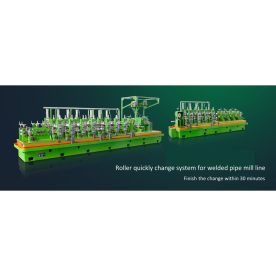
An In-Depth Guide to Tube Mill Production Line: Understanding Its Components, Benefits, and Applications in Modern Manufacturing
- **Improved Quality**: With advanced technology and quality control measures in place, tube mills consistently produce high-quality tubes that adhere to stringent standards. This level of quality assurance is critical in applications where structural integrity is paramount.
- **Sustainability**: Many tube mill production lines emphasize creating products that are recyclable and environmentally friendly. The processes often minimize energy consumption and waste, aligning with modern sustainability goals.
Applications of Tube Mill Production Lines
The versatility of tube mill production lines extends across various sectors:

An In-Depth Guide to Tube Mill Production Line: Understanding Its Components, Benefits, and Applications in Modern Manufacturing
- **Automotive**: The automotive industry relies on tube mills for manufacturing exhaust systems, chassis components, and other critical parts that require precision and durability.
- **Energy**: Pipeline construction for oil, gas, and water relies heavily on high-quality tubes produced by mill lines, ensuring safe and efficient transportation of resources.
- **Manufacturing Equipment**: Tubes are integral to many types of machinery and manufacturing equipment, from conveyors to hydraulic systems.
In conclusion, the tube mill production line stands as a cornerstone of modern manufacturing, offering efficiency, customization, and high quality. As industries continue to evolve, the innovations surrounding tube mills will undoubtedly play a pivotal role in meeting the demands of both traditional and emerging markets. Understanding its components and applications empowers manufacturers to harness the full potential of tube mill production lines, driving growth and sustainable practices across various sectors.