[Tube Mill Replacement Parts]Understanding the Importance of Tube Mill Replacement Parts: Ensuring Operational Efficiency and Longevity
News 2024-7-31
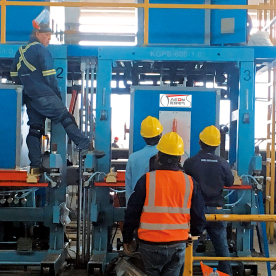
Understanding the Importance of Tube Mill Replacement Parts: Ensuring Operational Efficiency and Longevity
In the manufacturing industry, the functionality and reliability of equipment are paramount for maintaining operational efficiency and meeting production demands. Among the critical machinery used in various sectors, tube mills play a significant role in the production of tubular products that are essential in industries like construction, automotive, and transportation. To ensure that tube mills operate optimally, it is crucial to understand the importance of tube mill replacement parts. This article explores the significance of these parts, common types, and best practices for maintenance that can prolong the life of your tube mill operations.
The Role of Tube Mills in Manufacturing
Tube mills are specialized machines used for forming and welding metal sheets into tubes and pipes. They are designed to produce high-quality tubular products that meet stringent specifications. The process generally involves feeding flat metal sheets into the machine, which then bends the sheets into a cylindrical shape and welds the edges together. Given the high-speed nature of this operation, tube mills must be maintained in excellent working condition to ensure they can meet production demands without interruptions.
Importance of Tube Mill Replacement Parts
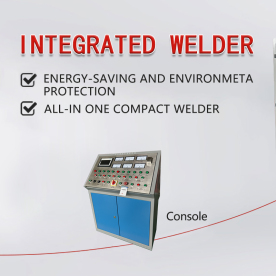
Understanding the Importance of Tube Mill Replacement Parts: Ensuring Operational Efficiency and Longevity
1. **Minimizing Downtime**: Regular wear can lead to unexpected breakdowns, causing significant downtime that can be costly for manufacturers. Having access to high-quality replacement parts allows for quick repairs, reducing downtime and keeping production on schedule.
2. **Improving Product Quality**: Worn or damaged components can affect the precision and quality of the welded seams, leading to defects in the tubular products. Replacing worn parts with new, high-quality replacements ensures that the end products meet the required standards and specifications.
3. **Cost Efficiency**: Investing in replacement parts can be more cost-effective than purchasing new machinery. By identifying and replacing only the worn components, manufacturers can extend the life of their equipment while avoiding the high costs associated with complete machinery replacement.
4. **Enhancing Safety**: Machines operating with worn components can become hazardous. Ensuring that all parts are in top condition provides a safer working environment for all employees, mitigating risks associated with machinery failures.
Common Tube Mill Replacement Parts
Understanding the specific components that typically need replacement can help manufacturers plan their maintenance schedules and parts inventory. Common tube mill replacement parts include:
- **Weld Rolls**: These are critical for the tube welding process. Over time, they can become misaligned or worn, necessitating replacement to maintain welding integrity.
- **Forming Rolls**: Used to shape the metal sheets into tubes, these rolls can wear down with use, causing issues in the tube forming process.
- **Drive Shafts**: These components are responsible for transmitting power from the drive motor to the various parts of the mill. They can fracture or suffer from wear and tear, affecting overall performance.
- **Bearings**: Bearings support rotating mechanisms in the tube mill and are subject to significant strain. Regular checks and timely replacements can prevent larger issues down the line.

Understanding the Importance of Tube Mill Replacement Parts: Ensuring Operational Efficiency and Longevity
Best Practices for Maintenance
To maximize the lifespan of tube mill replacement parts and ensure operational efficiency, manufacturers should adopt a proactive maintenance strategy:
1. **Regular Inspections**: Conduct routine inspections to identify signs of wear early. Catching potential issues before they develop into significant problems can save time and resources.
2. **Scheduled Replacements**: Implement a scheduled replacement program based on the wear patterns observed during inspections. This can help manufacturers anticipate needs and avoid unplanned downtime.
3. **Quality Parts**: Always invest in high-quality replacement parts. While cheaper options may seem appealing initially, they can lead to more problems and higher costs in the long run.
4. **Staff Training**: Make sure that operators are trained to recognize signs of wear and understand how to maintain the equipment properly. Knowledge of best practices can lead to better care and longevity of the machinery.
In conclusion, tube mill replacement parts are vital for maintaining efficiency, safety, and product quality in manufacturing operations. By understanding their importance and implementing proactive maintenance strategies, manufacturers can safeguard their investments in tube mill equipment and ensure a successful, uninterrupted production process.