[Solid state HF welder with temperature control]Revolutionizing Metal Joining: Exploring the Advantages of Solid State HF Welder with Temperature Control in Modern Manufacturing Processes
News 2024-7-31
In the ever-evolving landscape of manufacturing, the need for efficient, reliable, and precise joining techniques has never been more crucial. One innovative solution that has gained traction in recent years is the solid state HF welder with temperature control. This technology combines the benefits of high-frequency welding with advanced temperature management systems, resulting in improved performance, reduced defects, and enhanced overall manufacturing efficiency.
Understanding Solid State HF Welding
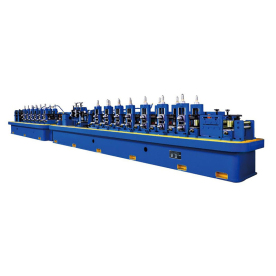
Revolutionizing Metal Joining: Exploring the Advantages of Solid State HF Welder with Temperature Control in Modern Manufacturing Processes
Solid state HF welders utilize a solid-state oscillator to generate high-frequency energy. This innovation creates a more consistent and reliable welding process compared to older vacuum or tube-based systems. Furthermore, solid-state devices are typically more energy-efficient, resulting in lower operational costs and a reduced environmental footprint.
The Role of Temperature Control
The integration of temperature control in solid state HF welders is transformative. Effective temperature management is critical in welding applications, as the temperature directly affects the quality of the weld. If the temperature is too high, it can lead to material degradation, while too low a temperature can result in weak welds with inadequate fusion.
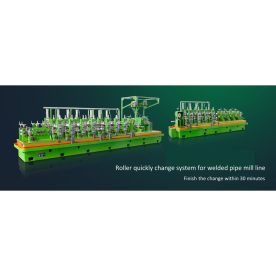
Revolutionizing Metal Joining: Exploring the Advantages of Solid State HF Welder with Temperature Control in Modern Manufacturing Processes
Advantages of Solid State HF Welders with Temperature Control
1. **Increased Precision**: The ability to control temperature precisely means that welders can work with a wider variety of materials and thicknesses without compromising quality. This precision is especially valuable in industries like automotive, aerospace, and medical devices, where the integrity of welds directly impacts performance and safety.
2. **Reduced Cycle Times**: Enhanced temperature control enables faster heating and cooling processes, decreasing overall cycle times. In high-volume production environments, this advantage translates to greater throughput and improved productivity, making businesses more competitive.

Revolutionizing Metal Joining: Exploring the Advantages of Solid State HF Welder with Temperature Control in Modern Manufacturing Processes
4. **Decreased Waste and Defects**: By achieving optimal temperature profiles during welding, companies can minimize the occurrence of defective products. Fewer defects lead to reduced waste and lower rework costs, directly impacting the bottom line.
5. **Enhanced Automation Compatibility**: Solid state HF welders can easily integrate with other automated systems. Temperature control mechanisms can synchronize with automated feeders and handling equipment, streamlining the manufacturing process and improving overall efficiency.
Applications in Various Industries
The versatility of solid state HF welders with temperature control makes them suitable for a multitude of industries. In the automotive sector, they are often used for joining plastic components, such as dashboards and interior panels. In the medical industry, precise welds are essential for producing high-quality medical devices and components that must meet stringent regulatory standards.
Moreover, in the electronics sector, manufacturers are increasingly relying on solid state HF welding for assembling delicate components where precision is paramount. The demand for lightweight materials in aerospace applications is also driving the adoption of this technology, as modern aircraft require reliable, lightweight welds to improve fuel efficiency.
Conclusion
As manufacturing continues to progress toward higher efficiency, lower costs, and enhanced quality, the solid state HF welder with temperature control stands out as a groundbreaking solution. By offering improved precision, reduced waste, and better energy efficiency, this technology is reshaping how manufacturers approach welding processes. As industries evolve, the adoption of these advanced welding technologies will undoubtedly play a pivotal role in achieving the next generation of manufacturing excellence.