[All-in-one High Frequency Welder for Automotive Industry]Revolutionizing Vehicle Manufacturing with the All-in-One High Frequency Welder: A Game Changer for the Automotive Industry
News 2024-7-30
In the rapidly evolving automotive industry, the need for innovative, efficient, and versatile manufacturing techniques is more critical than ever. As car manufacturers strive to enhance production speed while ensuring quality and durability, the All-in-One High Frequency Welder has emerged as a revolutionary tool that meets these demands. This cutting-edge welding technology integrates multiple welding processes into a single unit, empowering automotive manufacturers to streamline operations and achieve superior results.
Understanding High Frequency Welding
High frequency welding, also known as radio frequency welding, employs electromagnetic waves to generate heat, which fuses materials together. This technique is particularly effective for thermoplastic materials widely used in various automotive components, including bumpers, dashboards, and interior panels. By utilizing high-frequency welding, manufacturers can achieve strong, durable joints that maintain the structural integrity of the vehicle.
Versatility in Design and Production
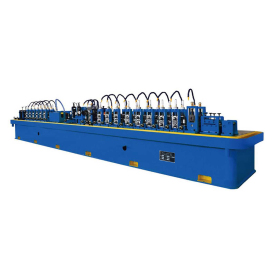
Revolutionizing Vehicle Manufacturing with the All-in-One High Frequency Welder: A Game Changer for the Automotive Industry
For instance, while traditional welding methods may require different machines for different processes, the All-in-One High Frequency Welder enables manufacturers to switch between processes seamlessly. This adaptability not only reduces the need for extensive machinery but also minimizes the time required for setup and production. By consolidating equipment, manufacturers can enhance their operational efficiency, ultimately leading to cost savings and increased output.
Enhanced Precision and Quality
In automotive manufacturing, precision is non-negotiable. The All-in-One High Frequency Welder is engineered to deliver consistent and uniform welds, resulting in high-quality finished products. This consistency is crucial, as even minor discrepancies in welding can lead to significant issues in vehicle performance and safety.
Furthermore, the high frequency welding process is less prone to the issues commonly associated with traditional methods, such as distortion or warping of materials. The controlled nature of high frequency welding ensures that the heat is applied precisely and evenly, preserving the original properties of the materials being joined. This level of precision is vital for components that are subject to rigorous safety standards and performance expectations.
Reducing Production Time and Costs
Time is money in the automotive industry, and the All-in-One High Frequency Welder helps manufacturers significantly reduce production time. The speed at which high frequency welding occurs allows for quicker cycle times, meaning that manufacturers can produce more components in less time. This expedited process is particularly beneficial when producing large volumes of parts, where efficiency translates directly into competitive pricing.
Moreover, by minimizing the number of machines needed for different welding processes, manufacturers can also cut down on maintenance costs and workforce training expenses. With fewer machines to manage, the operational burden is lighter, leaving teams free to focus on quality control and innovation.
Sustainability and Environmental Impact
As sustainability becomes an increasingly important focus for the automotive sector, the All-in-One High Frequency Welder also provides environmental benefits. The precision of the welding process minimizes waste material, and the ability to join dissimilar materials can lead to lighter vehicle designs. Lighter vehicles consume less fuel and reduce greenhouse gas emissions over their lifecycle.
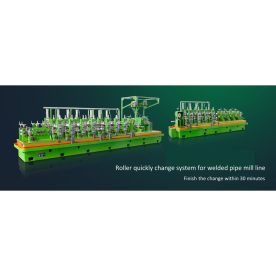
Revolutionizing Vehicle Manufacturing with the All-in-One High Frequency Welder: A Game Changer for the Automotive Industry

Revolutionizing Vehicle Manufacturing with the All-in-One High Frequency Welder: A Game Changer for the Automotive Industry
The All-in-One High Frequency Welder is more than just a trend; it is a transformative tool that addresses the pressing needs of the automotive industry. By enhancing versatility, precision, efficiency, and sustainability, this innovative welding solution empowers manufacturers to meet the challenges of modern vehicle production head-on. As the automotive industry continues to innovate and adapt, the adoption of advanced technologies like high frequency welding will be crucial for staying competitive and achieving long-term success.