[Roller for tube mill]Optimizing Production Efficiency: The Role of Roller for Tube Mill in Modern Manufacturing Processes
News 2024-7-29
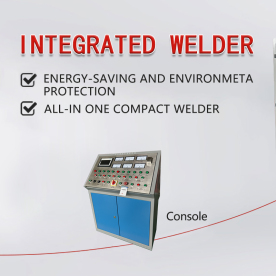
Optimizing Production Efficiency: The Role of Roller for Tube Mill in Modern Manufacturing Processes
Understanding the Tube Mill Process
A tube mill is a facility that transforms metal strips into cylindrical tubes through various stages of rolling and welding. The process involves feeding flat metal sheets, typically steel or aluminum, into the mill, where they are shaped and welded into tubes. The tube mill system comprises several components, including rollers, which are vital in shaping and guiding the material through the milling process.
The primary function of rollers in a tube mill is to deform the metal strips as they pass through. Rollers apply force to the material, causing it to bend and conform to the desired tubular shape. The specific arrangement, design, and engineering of these rollers directly influence the quality, strength, and consistency of the final product.
Types of Rollers Used in Tube Mills
In tube mills, various types of rollers are employed, each designed for specific functions throughout the milling process. Some of the most common types of rollers include:
1. **Forming Rollers**: These rollers are responsible for shaping the flat metal strips into a curved profile, preparing them for the final welding process. The design of forming rollers can vary significantly depending on the diameter and thickness of the tube being produced.
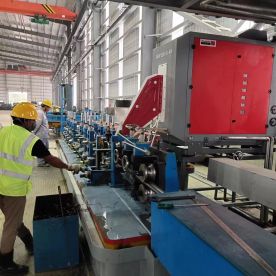
Optimizing Production Efficiency: The Role of Roller for Tube Mill in Modern Manufacturing Processes
3. **Finishing Rollers**: Once the tube is welded, finishing rollers work to refine the surface quality and dimensions of the tube. They help achieve the desired tolerances, ensuring that the final product meets industry standards and customer specifications.
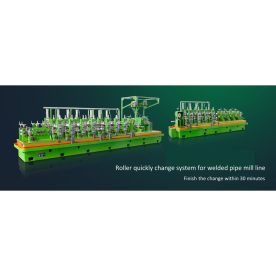
Optimizing Production Efficiency: The Role of Roller for Tube Mill in Modern Manufacturing Processes
Advances in Roller Technology
The advancements in roller technology have had a profound impact on the efficiency of tube mills. Modern rollers are often made from high-performance materials, such as tungsten carbide or heat-treated steel, providing enhanced durability and wear resistance. This leads to a longer lifespan for rollers, minimizing downtime and maintenance costs.
Additionally, innovations in roller design, including computer-aided design (CAD) and advanced simulation software, allow manufacturers to optimize roller profiles for specific applications. This can lead to improved flow rates, reduced energy consumption, and higher levels of product quality.
Another significant advancement is the integration of automation and smart technologies into roller operations. Sensors and digital monitoring systems can track performance metrics in real-time, allowing for immediate adjustments to the milling process. This enhances the precision and consistency of tube production, helping manufacturers meet increasingly stringent quality standards.
Conclusion
The roller for tube mill is a critical component in the manufacturing of tubes and pipes, playing a vital role in shaping the production process. With advancements in materials, design, and automation, today's roller technology enhances efficiency, reduces costs, and increases the quality of the final product. As the manufacturing industry continues to evolve, optimizing roller designs and integrating smart technologies will remain essential to maintaining competitiveness in the ever-demanding market. Investing in advanced roller technology is not merely a choice but a necessity for manufacturers aiming for excellence in the production of high-quality tubes and pipes.