[Precision Mould for Tube Mills]Transforming Tube Production: The Role of Precision Mould for Tube Mills in Advancing Manufacturing Efficiency and Product Quality
News 2024-7-29
****In the ever-evolving landscape of manufacturing, the production of steel tubes and pipes has increasingly relied on technology to enhance efficiency and output quality. One of the pivotal innovations in this sector is the use of precision moulds for tube mills. These advanced mould systems are designed to optimize the tube-forming process, ensuring that manufacturers can deliver high-quality products consistently, while also maximizing productivity and minimizing waste.
The Importance of Precision in Tube Manufacturing
The tube and pipe manufacturing industry serves a multitude of sectors, including construction, automotive, and energy. As these industries demand higher durability and performance from their materials, the need for precision in manufacturing becomes paramount. Everyday applications call for tubes that can withstand pressure, stress, and environmental factors. To meet these rigorous standards, manufacturers must rely on advanced tooling solutions that can produce tubes with exact dimensions and specifications.
Precision moulds are integral to this process. They help mold and shape the raw materials into specific pipe forms while providing the consistent dimensions required for various applications. A well-designed precision mould ensures that each tube meets the predetermined tolerances and quality expectations, thus reducing the likelihood of defects and rework.
How Precision Moulds Enhance Efficiency
The integration of precision moulds into tube mills drastically improves production efficiency. Traditionally, the tube manufacturing process involved extensive trial and error in mold creation, which could lead to high levels of waste and inefficiency. With precision mould technology, manufacturers can now achieve tighter tolerances and greater uniformity in their products, thus minimizing scrap materials and reducing costs.
Moreover, precision moulds are often designed for rapid changeovers. In an industry where production runs can vary greatly, the ability to swiftly adjust or replace moulds allows manufacturers to adapt quickly to different product specifications. This flexibility supports a lean manufacturing approach, where the goal is to maximize output while minimizing waste.
Quality Control Through Precision Mould Technology
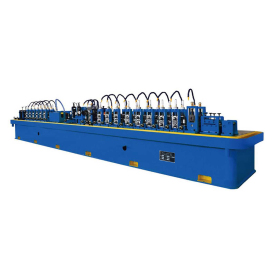
Transforming Tube Production: The Role of Precision Mould for Tube Mills in Advancing Manufacturing Efficiency and Product Quality
Manufacturers utilizing precision moulds can implement real-time quality checks during the production process. This allows for immediate identification of any deviations from product specifications, enabling swift corrective measures to be taken. Continuous monitoring not only improves product quality but also fosters a culture of accountability in manufacturing processes.
Innovative Manufacturing Solutions
The development of precision moulds for tube mills has also spurred innovation in the manufacturing sector. Many manufacturers are now exploring the use of computer-aided design (CAD) and computer-aided manufacturing (CAM) systems in the creation of moulds. These technologies enable more complex and effective mould designs, which can improve flow dynamics and thermal regulation during the production process.
In addition, 3D printing has started to play a role in the fabrication of precision moulds. This technology allows for rapid prototyping and the ability to produce intricate designs that were previously unachievable through traditional methods. As this technology matures, it is likely to further revolutionize the production of precision moulds for tube mills.
Sustainability and Environmental Impact
In today’s manufacturing environment, sustainability is an essential consideration. Precision mould technology supports sustainability initiatives by minimizing material waste, optimizing energy consumption, and extending the lifespan of moulds through superior design. These advantages align with the growing emphasis on environmental responsibility within the manufacturing sector, making precision moulds not just a choice for efficiency but also a step toward sustainable production practices.
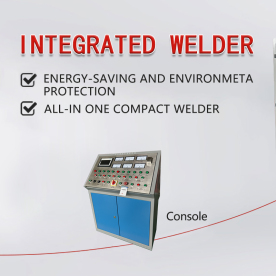
Transforming Tube Production: The Role of Precision Mould for Tube Mills in Advancing Manufacturing Efficiency and Product Quality
