[High-efficiency pipe mill production line]Maximizing Productivity and Quality: An In-Depth Look at High-Efficiency Pipe Mill Production Lines in Modern Manufacturing
News 2024-7-29
In today's fast-paced manufacturing environment, the demand for high-quality, durable pipes has surged, making the high-efficiency pipe mill production line an essential asset for industries ranging from construction to oil and gas. These advanced production lines not only enhance productivity but also ensure that the final products meet rigorous quality standards. In this article, we will explore the key components, benefits, and future trends of high-efficiency pipe mill production lines.
**Understanding High-Efficiency Pipe Mill Production Lines**
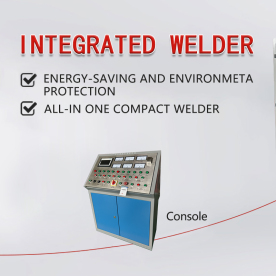
Maximizing Productivity and Quality: An In-Depth Look at High-Efficiency Pipe Mill Production Lines in Modern Manufacturing
The forming process involves shaping flat steel strips into cylindrical forms, which are then welded together using state-of-the-art welding technology. Recent advancements, such as high-frequency induction welding and laser welding, have further improved the efficiency and strength of the welded seams. After the welding process, the pipes undergo sizing and straightening, ensuring uniformity and adherence to specified dimensions.
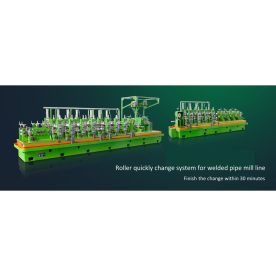
Maximizing Productivity and Quality: An In-Depth Look at High-Efficiency Pipe Mill Production Lines in Modern Manufacturing
**Key Benefits of High-Efficiency Pipe Mill Production Lines**
1. **Increased Productivity**: High-efficiency pipe mill production lines are designed for speed. Automation and advanced technologies enable manufacturers to produce a larger volume of pipes in a shorter time frame, significantly increasing overall production rates.
2. **Cost-Effectiveness**: While the initial investment in high-efficiency equipment may be higher, the return on investment (ROI) is realized through lower operational costs, reduced labor expenses, and minimized waste. Increased productivity translates into higher output without proportional increases in costs.
3. **Enhanced Quality**: Advanced manufacturing technologies incorporated into high-efficiency production lines ensure consistent quality. Automated inspections and real-time monitoring allow manufacturers to detect and correct issues quickly, preventing defective products from reaching customers.
4. **Flexibility and Customization**: Modern high-efficiency pipe mill production lines can be easily adapted to produce different types and sizes of pipes. This flexibility enables manufacturers to respond rapidly to market demands and customer specifications, whether for standard pipes or specialized variants.
5. **Sustainability**: Eco-friendliness is increasingly becoming a priority in manufacturing. High-efficiency production lines often incorporate energy-saving technologies and practices that minimize material waste and reduce the carbon footprint of pipe manufacturing.
**Future Trends in High-Efficiency Pipe Mill Production Lines**
As industries continue to evolve, so do the technologies used in high-efficiency pipe mill production lines. The future of pipe manufacturing is likely to be shaped by several key trends:

Maximizing Productivity and Quality: An In-Depth Look at High-Efficiency Pipe Mill Production Lines in Modern Manufacturing
2. **Advanced Materials**: The development of new materials, such as high-strength alloys and composites, will change the landscape of pipe production. This will require production lines to adapt to different forming and welding techniques to handle these materials effectively.
3. **Artificial Intelligence and Machine Learning**: The use of AI and machine learning algorithms will enhance the decision-making processes in production lines, optimizing operations and improving product quality.
4. **Customization and On-Demand Production**: As consumer preferences shift toward customization, production lines will need to accommodate smaller batch sizes and variable demand without compromising efficiency.
In conclusion, high-efficiency pipe mill production lines represent a significant advancement in manufacturing technology. By maximizing productivity, ensuring product quality, and embracing future trends, these production lines are poised to meet the growing demands of various industries while maintaining a focus on sustainability and operational excellence. As manufacturers continue to invest in these advanced systems, the future looks bright for the pipe production sector.