[High frequency welder equipment]Understanding High Frequency Welder Equipment: Essential Features, Applications, and Maintenance for Optimal Performance
News 2024-7-29
High frequency welding is a specialized process widely used in various industries to achieve strong and efficient joins in a range of materials. High frequency welder equipment plays a crucial role in this process, and understanding its features, applications, and maintenance is essential for any operation relying on welding technology. This article provides an in-depth look at high frequency welder equipment, exploring its core components, operational principles, applications across different sectors, and tips for proper maintenance to ensure longevity and performance.
What is High Frequency Welding?
High frequency welding involves the use of high-frequency electrical currents to weld metals and plastics. The process is particularly beneficial for materials that require rapid heating and precise joining techniques. High frequency welder equipment typically utilizes electromagnetic fields to generate heat in the workpieces, allowing them to fuse together without the need for additional filler materials.
Core Components of High Frequency Welder Equipment
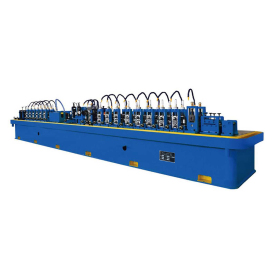
Understanding High Frequency Welder Equipment: Essential Features, Applications, and Maintenance for Optimal Performance
2. **Electrodes**: The electrodes play a critical role in the welding process, as they conduct the high-frequency currents to the workpieces. The design and material of the electrodes can significantly affect the quality of the weld.
3. **Cooling System**: During operation, the equipment can generate a substantial amount of heat. A reliable cooling system, often involving water or air cooling, is essential to maintain optimal operating temperatures and prevent damage to the machinery.
4. **Control Panel**: Modern high frequency welders come equipped with sophisticated control panels that allow operators to adjust settings such as frequency, power output, and operational modes. These features improve precision and ensure that the welding parameters meet the specific requirements of different applications.
5. **Safety Features**: Safety is paramount in any industrial setting. High frequency welder equipment typically includes several safety features such as emergency stop buttons, protective guards, and electrical safeguards to protect both the operator and equipment.
Applications of High Frequency Welder Equipment
High frequency welder equipment is versatile and finds applications across various industries:
- **Plastic Manufacturing**: One of the most prominent applications of high frequency welding is in the production of plastic products. Industries manufacturing items like PVC tarps, inflatable boats, and automotive parts often rely on high frequency welders to achieve strong, durable seams.
- **Textile Industry**: High frequency welding is also widely used in the textile industry, particularly for creating waterproof seams in outdoor gear, tents, and inflatable products such as air mattresses.
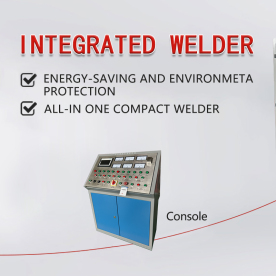
Understanding High Frequency Welder Equipment: Essential Features, Applications, and Maintenance for Optimal Performance
- **Metal Fabrication**: High frequency welding is applicable in metal fabrication, especially for joining thin sheets of metal. The technique allows for quick welding processes without the need for additional materials.
Maintenance of High Frequency Welder Equipment
Proper maintenance of high frequency welder equipment is critical to ensure optimal performance and longevity. Here are some key maintenance tips:
1. **Regular Inspections**: Routine inspections of the equipment can help detect early signs of wear or damage. Check for any abnormal noises, excessive heat, or irregular readings on the control panel.
2. **Clean the Equipment**: Dust and debris can accumulate on the equipment, affecting its performance. Regular cleaning of the components, particularly the electrodes and cooling system, is essential.
3. **Check Electrical Connections**: Ensure that all electrical connections remain secure and free from corrosion. Loose connections can lead to equipment malfunction and unsafe operating conditions.
4. **Monitor Cooling Systems**: Regularly check the cooling system to ensure it is functioning properly. Overheating can lead to serious damage and operational downtime.
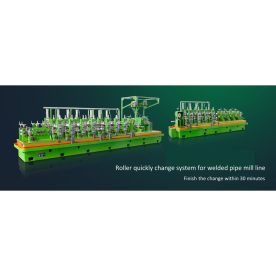
Understanding High Frequency Welder Equipment: Essential Features, Applications, and Maintenance for Optimal Performance
Conclusion
High frequency welder equipment is indispensable in various production and fabrication processes, providing efficient and reliable welding solutions. Understanding its features, applications, and maintenance requirements is essential for industries that rely on this technology. By investing in quality equipment and adhering to maintenance best practices, companies can ensure the effectiveness of their welding operations and enhance overall productivity.