[Industrial All-in-one High Frequency Welder]Exploring the Advancements of Industrial All-in-one High Frequency Welder: Revolutionizing Fabrication and Manufacturing Processes
News 2024-7-29
In the ever-evolving landscape of manufacturing and fabrication, the role of welding technologies cannot be overstated. Among the groundbreaking innovations, the Industrial All-in-one High Frequency Welder stands as a key player, facilitating superior welding processes that meet the demands of diverse industries. This comprehensive article aims to delve into the functionalities, advantages, and multifaceted applications of the Industrial All-in-one High Frequency Welder, shedding light on how it is revolutionizing production efficiency and quality.
Understanding High Frequency Welding Technology
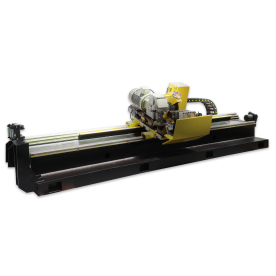
Exploring the Advancements of Industrial All-in-one High Frequency Welder: Revolutionizing Fabrication and Manufacturing Processes
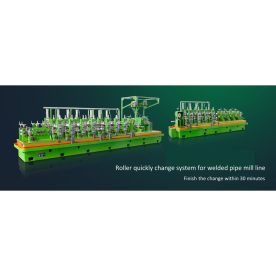
Exploring the Advancements of Industrial All-in-one High Frequency Welder: Revolutionizing Fabrication and Manufacturing Processes
One of the defining characteristics of the Industrial All-in-one High Frequency Welder is its versatility. Typically, these welders are equipped to handle various welding techniques such as butt welding, lap welding, and seam welding. The welder's ability to work with different materials, including stainless steel, aluminum, and polymers, makes it suitable for a wide range of manufacturing processes.
**1. User-Friendly Control Systems:** Modern Industrial All-in-one High Frequency Welders are designed with intuitive control systems, often featuring touchscreens that allow operators to easily set parameters such as heating temperature, welding speed, and pressure. This not only minimizes training time for new operators but also enhances the precision of the welding process.
**2. Compact and Space-Efficient Design:** Unlike traditional welding setups that can be bulky and cumbersome, the all-in-one design of these welders saves valuable floor space in manufacturing settings. Their compact size also makes them portable, facilitating easier transport between different workstations.

Exploring the Advancements of Industrial All-in-one High Frequency Welder: Revolutionizing Fabrication and Manufacturing Processes
**4. Enhanced Weld Quality:** The localized heating provided by high-frequency welding technology ensures that welds are clean, strong, and free from the imperfections often associated with traditional welding methods. This leads to better product quality and longevity, which is critical in industries such as aerospace, automotive, and construction.
Applications Across Industries
The versatility of the Industrial All-in-one High Frequency Welder makes it a valuable asset across various sectors. In the automotive industry, these welders are employed to join metal components with precision, ensuring structural integrity and safety in vehicles. In the aerospace sector, where weight reduction is essential, they are utilized for creating lightweight but strong components.
Moreover, in the textile and packaging industries, high-frequency welding is used to create seams in synthetic fabrics and films, contributing to effective sealing and durability. The electronics sector also benefits, as these welders can adeptly handle fine electronic components that require precise welding without affecting surrounding parts.
Conclusion
The Industrial All-in-one High Frequency Welder represents a significant enhancement in welding technology, characterized by its adaptability, efficiency, and unparalleled weld quality. As industries continue to seek ways to optimize production processes and improve product integrity, the importance of such advanced equipment cannot be underestimated. By adopting the Industrial All-in-one High Frequency Welder, manufacturers position themselves at the forefront of innovation, paving the way for a robust and competitive future in fabrication and manufacturing. The integration of high-frequency welding technology not only streamlines operations but also propels industries toward higher standards of quality, efficiency, and sustainability.