[Integrated pipe mill production line system]Understanding the Integrated Pipe Mill Production Line System: A Comprehensive Overview of Its Components and Benefits
News 2024-7-27
****In today's highly competitive manufacturing landscape, the efficiency and effectiveness of production systems are paramount for success. The integrated pipe mill production line system plays a crucial role in streamlining the production process of pipes, ensuring that manufacturers can meet customer demands while maintaining high standards of quality. This article delves into the key components, functionalities, and benefits of an integrated pipe mill production line system, highlighting how it enhances operational performance and drives innovation in the piping industry.
What is an Integrated Pipe Mill Production Line System?
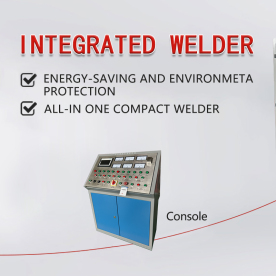
Understanding the Integrated Pipe Mill Production Line System: A Comprehensive Overview of Its Components and Benefits
Key Components of the System
1. **Raw Material Preparation**: The production process begins with the preparation of raw materials—typically coils of steel. This stage involves unwinding and cutting the steel to the appropriate dimensions for the pipe being produced.
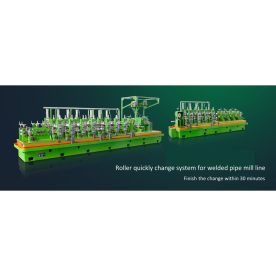
Understanding the Integrated Pipe Mill Production Line System: A Comprehensive Overview of Its Components and Benefits
3. **Welding Station**: The next step involves welding, where edges of the formed pipe are joined together using high-frequency induction welding or other welding techniques. This is a critical phase to ensure the integrity and strength of the pipe.
4. **Sizing Mill**: Following the welding process, the pipe moves to the sizing mill, which adjusts the dimensions of the pipe to meet specific requirements. This station ensures uniformity in size and alignment, which is essential for quality control.

Understanding the Integrated Pipe Mill Production Line System: A Comprehensive Overview of Its Components and Benefits
6. **Testing and Quality Control**: An integrated system incorporates rigorous testing protocols throughout the production process. Non-destructive testing techniques may be employed to identify any defects or weaknesses in the pipe, ensuring high-quality output.
Benefits of an Integrated Pipe Mill Production Line System
1. **Enhanced Efficiency**: By integrating various stages of production into a single system, manufacturers can minimize the time and resources spent on transitioning between different processes. This integration leads to smoother operations and faster production cycles.
2. **Consistent Quality**: An integrated approach allows for better control over the production process, resulting in more consistent product quality. Continuous monitoring and testing at each stage of the production line contribute to minimizing defects and variances.
3. **Flexibility and Customization**: Modern integrated pipe mill systems are designed to be adaptable to various production requirements. Manufacturers can easily adjust parameters to accommodate different pipe sizes, lengths, and material specifications without significant downtime.
4. **Cost-Effectiveness**: With reduced waste, improved resource allocation, and minimized labor costs, an integrated pipe mill production line system can lead to significant cost savings for manufacturers. The efficiency gains often result in a higher return on investment.
5. **Environmental Sustainability**: Integrated systems can utilize advanced technologies, including energy-efficient processes and waste reduction measures. As a result, manufacturers can operate in a more environmentally responsible manner, aligning with global sustainability goals.
Conclusion
The integrated pipe mill production line system represents a significant advancement in the manufacturing of pipes. Its ability to combine multiple production stages into a cohesive framework not only enhances efficiency and quality but also empowers manufacturers to remain competitive in a fast-evolving market. As industries focus more on innovation and sustainability, investing in such systems becomes increasingly vital for long-term success. With the continuous evolution of technology, the future of integrated pipe mill production line systems remains promising, poised to contribute profoundly to the efficiency and sustainability of the global piping industry.